Welded pipe forming production line
A production line and welded pipe technology, which is applied in the field of production equipment and steel pipe manufacturing, can solve the problems of high raw material cost, low production efficiency, large raw material, etc., and achieve the effect of reducing raw material cost, improving production efficiency and avoiding waste
- Summary
- Abstract
- Description
- Claims
- Application Information
AI Technical Summary
Problems solved by technology
Method used
Image
Examples
Embodiment Construction
[0034] The specific embodiments of the present invention will be described below with reference to the accompanying drawings.
[0035] like figure 1 As shown in the figure, the welded pipe forming production line of the present invention is arranged on the first bed 1 and the second bed 2, and includes a guiding and leveling section 3, a forming section 4, a welding section 5, a welding section 5, and a welding section arranged in sequence from front to back. Treatment section 6 and sizing section 7; after the welded pipe is welded and formed in welding section 5, the outer burr is first removed, and then enters the welding seam post-processing section 6, followed by preliminary extrusion, inner burr treatment, and further extrusion treatment. heat treatment.
[0036] like figure 1 , figure 2 As shown, the forming section 4 is arranged on the first bed 1 and the second bed 2, and a number of forming gantry are arranged in sequence, and each forming gantry is provided with ...
PUM
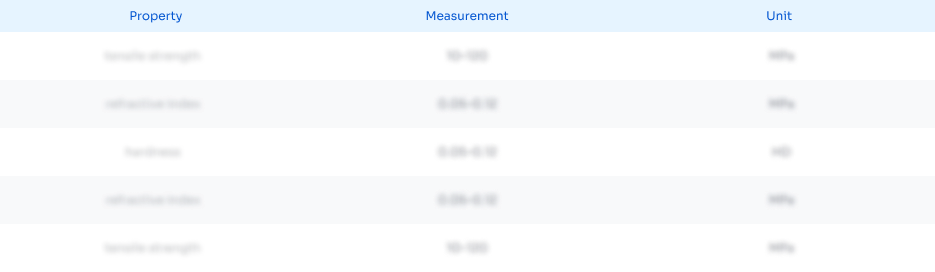
Abstract
Description
Claims
Application Information

- Generate Ideas
- Intellectual Property
- Life Sciences
- Materials
- Tech Scout
- Unparalleled Data Quality
- Higher Quality Content
- 60% Fewer Hallucinations
Browse by: Latest US Patents, China's latest patents, Technical Efficacy Thesaurus, Application Domain, Technology Topic, Popular Technical Reports.
© 2025 PatSnap. All rights reserved.Legal|Privacy policy|Modern Slavery Act Transparency Statement|Sitemap|About US| Contact US: help@patsnap.com