Crankshaft dynamic balancing machine
A dynamic balancing machine and crankshaft technology, which is applied in static/dynamic balance testing, machine/structural components testing, instruments, etc., can solve the problem of asymmetric weight distribution center, unbalance, and affecting three-cylinder crankshaft dynamic balance verification Accuracy and other issues to achieve the effect of improving accuracy and expanding the scope of application
- Summary
- Abstract
- Description
- Claims
- Application Information
AI Technical Summary
Problems solved by technology
Method used
Image
Examples
Embodiment Construction
[0034] The following is attached Figure 1-8 The application is described in further detail.
[0035] The embodiment of the application discloses a crankshaft dynamic balancing machine. refer to figure 1A crankshaft dynamic balancing machine includes a swing frame 1, a support mechanism 2 and a drive mechanism 3 are sequentially arranged above the swing frame 1, and a detection mechanism 4 is arranged at the bottom of the swing frame 1. When performing dynamic balance check on the three-cylinder crankshaft 01, place the three-cylinder crankshaft 01 on the support mechanism 2, use the support mechanism 2 to support it, and then use the drive mechanism 3 to drive the three-cylinder crankshaft 01 to rotate. During the rotation The detection mechanism 4 monitors the rotation state of the three-cylinder crankshaft 01, and performs a dynamic balance check on the three-cylinder crankshaft 01.
[0036] refer to figure 2 and image 3 , the support mechanism 2 includes two support...
PUM
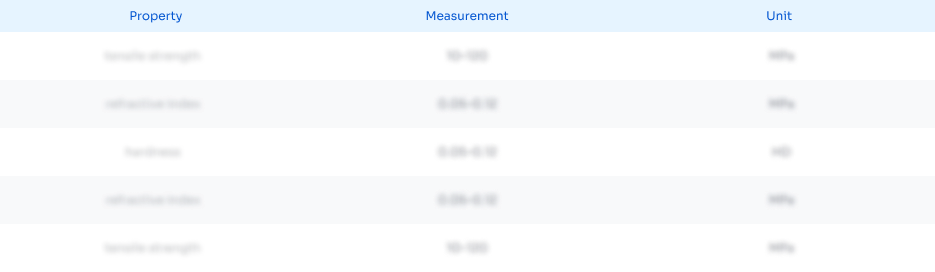
Abstract
Description
Claims
Application Information

- R&D
- Intellectual Property
- Life Sciences
- Materials
- Tech Scout
- Unparalleled Data Quality
- Higher Quality Content
- 60% Fewer Hallucinations
Browse by: Latest US Patents, China's latest patents, Technical Efficacy Thesaurus, Application Domain, Technology Topic, Popular Technical Reports.
© 2025 PatSnap. All rights reserved.Legal|Privacy policy|Modern Slavery Act Transparency Statement|Sitemap|About US| Contact US: help@patsnap.com