Shield segment deformation monitoring system and monitoring method thereof
A shield segment and deformation monitoring technology, which is applied to measuring devices, instruments, optical devices, etc., can solve the problems of difficult installation and disassembly, incompatibility, and complex connection of cables, so as to reduce disassembly and installation steps, Improve monitoring efficiency and ensure the effect of battery life
- Summary
- Abstract
- Description
- Claims
- Application Information
AI Technical Summary
Problems solved by technology
Method used
Image
Examples
Embodiment 1
[0071] Example 1, such as Figure 1 to Figure 5 As shown, the shield segment deformation monitoring system described in this application includes multiple sets of laser sensing modules arranged along the shield segment propped up and constituting the frame section tunnel, as well as an automatic total station and a data processing platform;
[0072] Wherein, adjacent two groups of laser sensing modules are separated by at least one group of shield segments, and each group includes a CCD laser receiving target 1, a laser transmitter 2 and a data collector 3;
[0073] The CCD laser receiving target 1 is vertically fixed on the data collector 3 through the slot 6, and an attenuation sheet is installed on the CCD laser receiving target 1 to weaken the light intensity;
[0074] The laser transmitter 2 is fixed on the data collector 3 through the support 4;
[0075] Several vacuum chucks 5 are arranged at the bottom of the data collector 3 , and the laser sensing module is fixed on...
PUM
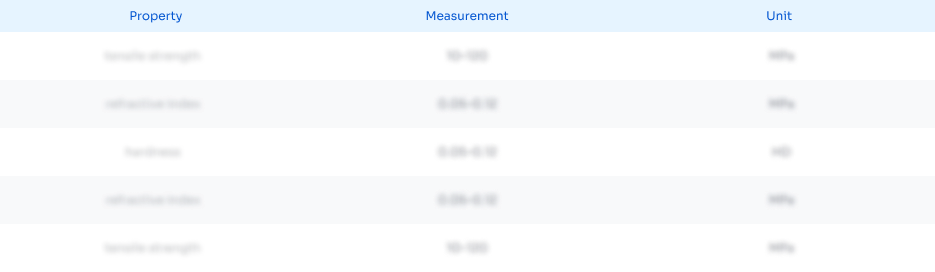
Abstract
Description
Claims
Application Information

- R&D
- Intellectual Property
- Life Sciences
- Materials
- Tech Scout
- Unparalleled Data Quality
- Higher Quality Content
- 60% Fewer Hallucinations
Browse by: Latest US Patents, China's latest patents, Technical Efficacy Thesaurus, Application Domain, Technology Topic, Popular Technical Reports.
© 2025 PatSnap. All rights reserved.Legal|Privacy policy|Modern Slavery Act Transparency Statement|Sitemap|About US| Contact US: help@patsnap.com