Light three-translation robot
A three-translation and robot technology, which is applied in the direction of manipulators, program-controlled manipulators, and object stacking, can solve the problems of large weight, large size, and heavy metal rods, etc., to reduce size and weight, improve work Space, the effect of reducing its own weight
- Summary
- Abstract
- Description
- Claims
- Application Information
AI Technical Summary
Problems solved by technology
Method used
Image
Examples
Embodiment Construction
[0022] Such as Figure 1-Figure 4As shown, a light-duty three-translational robot includes a rotating arm, a large arm, a small arm and a wrist 14. The rotating arm includes a robot base 1, a waist base 2 and a first axis motor 3. The inside of the robot base 1 is hollow, and the reducer is installed On the upper part of the robot base 1, the reducer is a harmonic reducer, which occupies a small space; the lower part of the robot base 1 is used to connect the robot mounting seat, and the output end of the first axis motor 3 is fixed to the input end of the reducer. Connected, the output end of the reducer is fixedly connected with one end of the waist seat 2, the first axis motor 3 drives the waist seat 2 to rotate around one end, the rotating shaft of the waist seat 2 rotating around one end is the rotating shaft a, and the rotating shaft A is connected to the first shaft motor 3 of the rotating shafts; the boom includes the first installation vertical plate 6, the second axi...
PUM
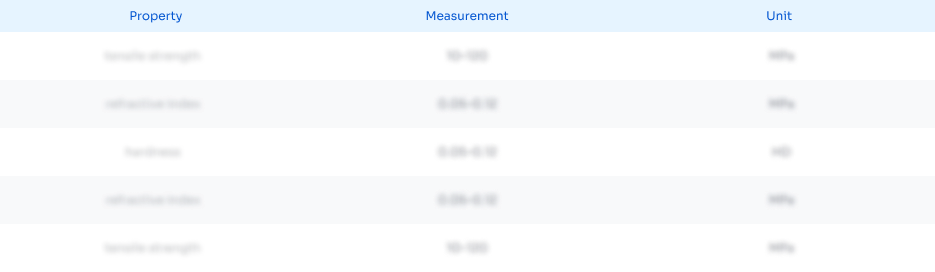
Abstract
Description
Claims
Application Information

- R&D
- Intellectual Property
- Life Sciences
- Materials
- Tech Scout
- Unparalleled Data Quality
- Higher Quality Content
- 60% Fewer Hallucinations
Browse by: Latest US Patents, China's latest patents, Technical Efficacy Thesaurus, Application Domain, Technology Topic, Popular Technical Reports.
© 2025 PatSnap. All rights reserved.Legal|Privacy policy|Modern Slavery Act Transparency Statement|Sitemap|About US| Contact US: help@patsnap.com