Composite nanofiltration membrane as well as preparation method and application thereof
A composite nanofiltration membrane and base membrane technology, applied in the field of composite membranes, can solve problems such as low permeation flux and poor solvent resistance, and achieve high permeation flux, high separation performance, and simple preparation process
- Summary
- Abstract
- Description
- Claims
- Application Information
AI Technical Summary
Problems solved by technology
Method used
Image
Examples
preparation example 1
[0058] Preparation of Chlorinated Polyvinyl Chloride:
[0059] According to the document "Research on Preparation of Chlorinated Polyvinyl Chloride by Aqueous Phase Suspension Method" [D]. Chen Guowen. Zhejiang: Zhejiang University, 2013, the prepared chlorinated polyvinyl chloride meets the requirements of HG / T 4346-2012 coating Standard for Chlorinated Polyvinyl Chloride Resins. The weight average molecular weight is 200000-500000.
Embodiment 1
[0061] (1) Mix chlorinated polyvinyl chloride with N,N-dimethylacetamide, wherein, based on the total weight of chlorinated polyvinyl chloride and N,N-dimethylacetamide, chlorinated polyvinyl chloride The content is 25% by weight, then stirred in a 90°C water bath for 4 hours, left to cool to 20°C, put it into a desiccator for degassing for 3 hours, and made a casting solution;
[0062] (2) Evenly apply (scrape) the cast film solution to the polypropylene non-woven fabric fixed on the glass plate with a stainless steel scraper, control the distance between the knife edge and the non-woven fabric to be 100 μm, and immediately put the scraped film in 25 In the gel bath of the deionized water of ℃, after 1 hour, take out from the gel bath, and take off from the glass plate, after the casting liquid is solidified, immerse in the hexamethylenediamine solution of 6% by weight, Then refrigerate to obtain the support layer, and the side of the non-woven fabric scraping the casting liq...
Embodiment 2
[0070] (1) Mix chlorinated polyvinyl chloride with N,N-dimethylacetamide, wherein, based on the total weight of chlorinated polyvinyl chloride and N,N-dimethylacetamide, chlorinated polyvinyl chloride The content is 15% by weight, then stirred in a 90°C water bath for 4 hours, left to cool to 20°C, put it into a desiccator for degassing for 3 hours, and made a casting solution;
[0071] (2) Evenly apply (scrape) the cast film solution to the polypropylene non-woven fabric fixed on the glass plate with a stainless steel scraper, control the distance between the knife edge and the non-woven fabric to be 100 μm, and immediately put the scraped film in 25 In the gel bath of the deionized water of ℃, after 1 hour, take out from the gel bath, and take off from the glass plate, after the casting liquid is solidified, immerse in the hexamethylenediamine solution of 6% by weight, Then refrigerate to obtain the support layer, and the side of the non-woven fabric scraping the casting liq...
PUM
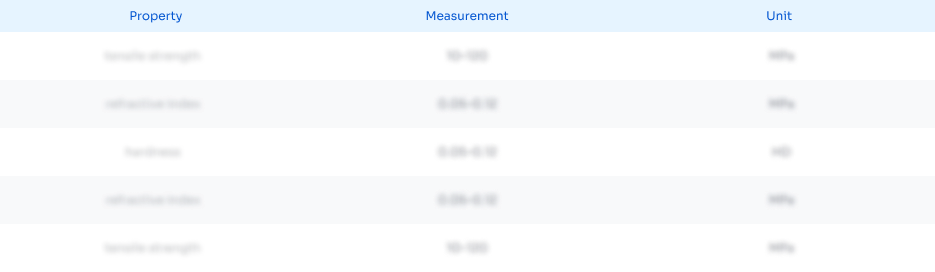
Abstract
Description
Claims
Application Information

- Generate Ideas
- Intellectual Property
- Life Sciences
- Materials
- Tech Scout
- Unparalleled Data Quality
- Higher Quality Content
- 60% Fewer Hallucinations
Browse by: Latest US Patents, China's latest patents, Technical Efficacy Thesaurus, Application Domain, Technology Topic, Popular Technical Reports.
© 2025 PatSnap. All rights reserved.Legal|Privacy policy|Modern Slavery Act Transparency Statement|Sitemap|About US| Contact US: help@patsnap.com