SiO2@metal-organic nanosheet core-shell material, preparation process and catalytic performance detection method
A nanosheet and core-shell technology, applied in the field of materials engineering and catalysts, can solve the problems of small overall size, small size and thickness, and low recycling rate, and achieve the effects of low cost, simple operation, and improved catalytic conversion efficiency
- Summary
- Abstract
- Description
- Claims
- Application Information
AI Technical Summary
Problems solved by technology
Method used
Image
Examples
Embodiment 1
[0103] Take 50 mg of carboxyl-functionalized silica spheres and 10 mg of zirconium tetrachloride and disperse them in 34.5 mL of DMF. After ultrasonic dissolution, add 1 mL of deionized water and 4.5 mL of formic acid. Shake at 120°C for 24 hours. Then add 154 mg of tricarboxylic acid ligand, and continue shaking at 120 °C for 48 h; after the shaking is over, centrifuge to remove the supernatant, wash with deionized water three times, and dry in vacuum at 60 °C for 24 h to obtain a spherical silicon-based metal-organic composite Material. After shaking, the supernatant was removed by centrifugation, washed three times with deionized water, and dried in vacuum at 60°C for 24 hours to obtain spherical SiO 2 @metal-organic nanosheet core-shell materials. Through the ICP test, the content of Zr is 1.63%, and the calculated mass percentage of MOF nanosheet material is 17.7%.
Embodiment 2
[0105] Take 45 mg of carboxyl-functionalized silica spheres and 10 mg of zirconium tetrachloride and disperse them in 34.5 mL of DMF. After ultrasonic dissolution, add 1 mL of deionized water and 4.5 mL of formic acid. Shake at 120°C for 24 hours. Then add 154 mg of tricarboxylic acid ligand, and continue shaking at 120 °C for 48 h; after the shaking is over, centrifuge to remove the supernatant, wash with deionized water three times, and dry in vacuum at 60 °C for 24 h to obtain a spherical silicon-based metal-organic composite Material. After shaking, the supernatant was removed by centrifugation, washed three times with deionized water, and dried in vacuum at 60°C for 24 hours to obtain spherical SiO 2 @metal-organic nanosheet core-shell materials. Through the ICP test, the content of Zr is 2.33%, and the calculated mass percentage of MOF nanosheet material is 25.1%.
Embodiment 3
[0107] Take 50 mg of carboxyl-functionalized silica spheres and 10 mg of zirconium tetrachloride and disperse them in 34.5 mL of DMF. After ultrasonic dissolution, add 1 mL of deionized water and 4.5 mL of formic acid. Shake at 110°C for 24 hours. Then add 150 mg of tricarboxylic acid ligand, and continue shaking at 110 °C for 48 h; after the shaking is over, centrifuge to remove the supernatant, wash with deionized water three times, and vacuum dry at 60 °C for 24 h to obtain a spherical silicon-based metal-organic composite Material. After shaking, the supernatant was removed by centrifugation, washed three times with deionized water, and dried in vacuum at 60°C for 24 hours to obtain spherical SiO 2 @metal-organic nanosheet core-shell materials. Through the ICP test, the content of Zr is 1.06%, and the calculated mass percentage of MOF nanosheet material is 10.5%.
PUM
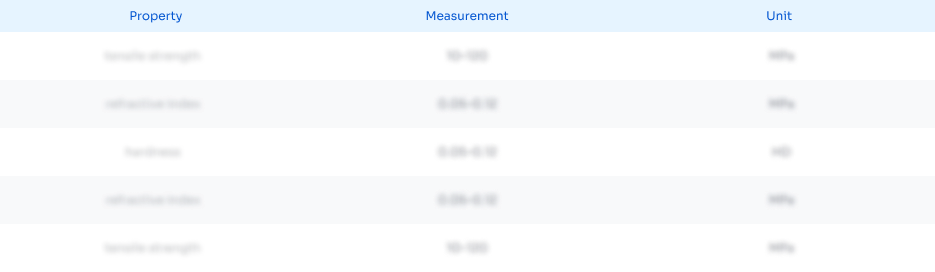
Abstract
Description
Claims
Application Information

- R&D Engineer
- R&D Manager
- IP Professional
- Industry Leading Data Capabilities
- Powerful AI technology
- Patent DNA Extraction
Browse by: Latest US Patents, China's latest patents, Technical Efficacy Thesaurus, Application Domain, Technology Topic, Popular Technical Reports.
© 2024 PatSnap. All rights reserved.Legal|Privacy policy|Modern Slavery Act Transparency Statement|Sitemap|About US| Contact US: help@patsnap.com