Method for assembling trigger component of submachine gun
A technology for a submachine gun and a trigger, applied in the field of submachine guns, can solve the problems of increasing the failure rate of submachine guns, difficult to master the assembly method, and dare not to easily decompose iron-resistant parts, etc., and achieves good economic and social benefits, convenient and fast assembly operation, and good promotion. and practical value
- Summary
- Abstract
- Description
- Claims
- Application Information
AI Technical Summary
Problems solved by technology
Method used
Image
Examples
Embodiment Construction
[0038] Below in conjunction with the accompanying drawings the present invention is further described, in the accompanying drawings, 1-replacement pin, 2-blocking iron spring limit lever, 3-trigger, 4-trigger spring, 5-single-shot sear, 6-blocking iron spring, 7-assembly sleeve, 8-block iron spring limit base; 101-conical tip, 102-conical guide section, 103-right angle positioning shoulder, 104-assembly sleeve installation section, 105-second transition section, 106-first transition section, 201-limit guide section, 202-limit section, 203-external thread connection section, 301-installation hole 1 of upper assembly sleeve on trigger, 302-installation hole 2 of upper assembly sleeve on trigger, 303-trigger Limiting hole of the upper resistance iron spring, 304-process hole of the upper resistance iron spring of the trigger, 401-inner torsion arm of the trigger spring, 402-inner hole of the cylindrical spiral of the trigger spring, 403-the first outer torsion arm of the trigger s...
PUM
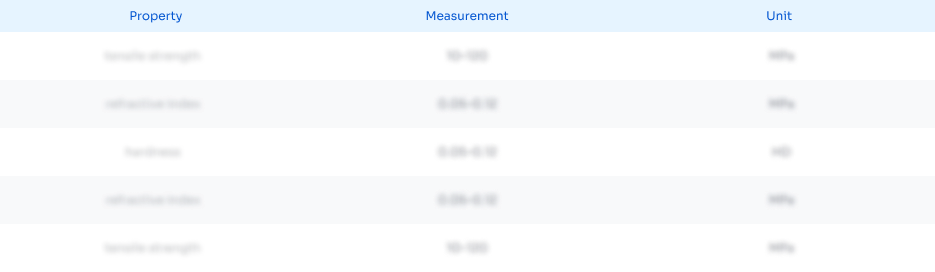
Abstract
Description
Claims
Application Information

- R&D
- Intellectual Property
- Life Sciences
- Materials
- Tech Scout
- Unparalleled Data Quality
- Higher Quality Content
- 60% Fewer Hallucinations
Browse by: Latest US Patents, China's latest patents, Technical Efficacy Thesaurus, Application Domain, Technology Topic, Popular Technical Reports.
© 2025 PatSnap. All rights reserved.Legal|Privacy policy|Modern Slavery Act Transparency Statement|Sitemap|About US| Contact US: help@patsnap.com