Multi-sensor parallel type force value measuring method
A measurement method and multi-sensor technology, applied in force/torque/work measuring instruments, measuring devices, instruments, etc., can solve the problem that the force sensor cannot be guaranteed uniform force.
- Summary
- Abstract
- Description
- Claims
- Application Information
AI Technical Summary
Problems solved by technology
Method used
Image
Examples
Embodiment Construction
[0016] Embodiments of the multi-sensor parallel force measurement method in the present invention are as follows: Figure 1~2 As shown: the method includes the following steps. In the first step, a test press whose output force value matches the measurement range of a single force sensor 5 is selected to apply pressure to a single force sensor. Calculate the elastic coefficient k of the force sensor under the pressure; the second step, select four force sensors 5 with the same elastic coefficient for pressure detection of the press to be measured, each force sensor 5 is vertically arranged side by side, each force sensor, along the Circumferentially arranged in sequence, adjust the height of the top force point 4 of each force sensor to be consistent. In the third step, the indenter 10 of the press to be measured applies pressure to the top force point 4 of each force sensor through the force transmission plate.
[0017] In the first step above, the matching of the output forc...
PUM
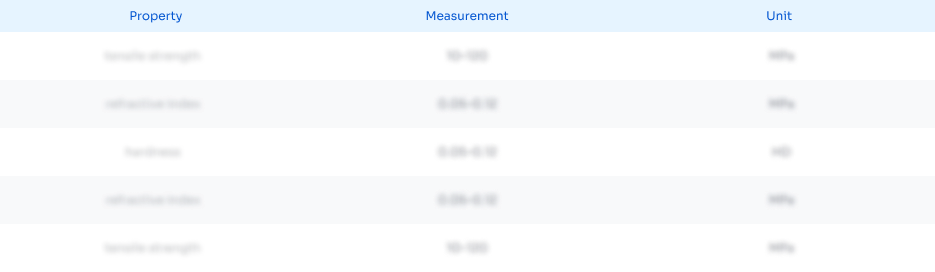
Abstract
Description
Claims
Application Information

- R&D
- Intellectual Property
- Life Sciences
- Materials
- Tech Scout
- Unparalleled Data Quality
- Higher Quality Content
- 60% Fewer Hallucinations
Browse by: Latest US Patents, China's latest patents, Technical Efficacy Thesaurus, Application Domain, Technology Topic, Popular Technical Reports.
© 2025 PatSnap. All rights reserved.Legal|Privacy policy|Modern Slavery Act Transparency Statement|Sitemap|About US| Contact US: help@patsnap.com