Mechanical arm fine adjustment control quantity interpretation method and computer readable storage medium
A technology of mechanical arm and control quantity, which is applied in the field of measurement and control, can solve the problems of high professional requirements for use and maintenance, strong professional requirements, and small working range, etc., and achieve low volume, weight and energy consumption of equipment, strong work adaptability, and adaptability The effect of flexibility
- Summary
- Abstract
- Description
- Claims
- Application Information
AI Technical Summary
Problems solved by technology
Method used
Image
Examples
Embodiment Construction
[0024] The specific embodiments of the present invention will be described in detail below in conjunction with the accompanying drawings, but it should be understood that the protection scope of the present invention is not limited by the specific embodiments.
[0025]Unless expressly stated otherwise, throughout the specification and claims, the term "comprise" or variations thereof such as "includes" or "includes" and the like will be understood to include the stated elements or constituents, and not Other elements or other components are not excluded.
[0026] In order to overcome the problems of the prior art, the present invention proposes a method for interpreting the fine-tuned control amount of the manipulator. On the premise that the imaging area has target reference scales and reference marker points arranged perpendicular to the optical axis (such as two features Points, or circles, rectangles and other feature marks), according to the comparison and interpretation ...
PUM
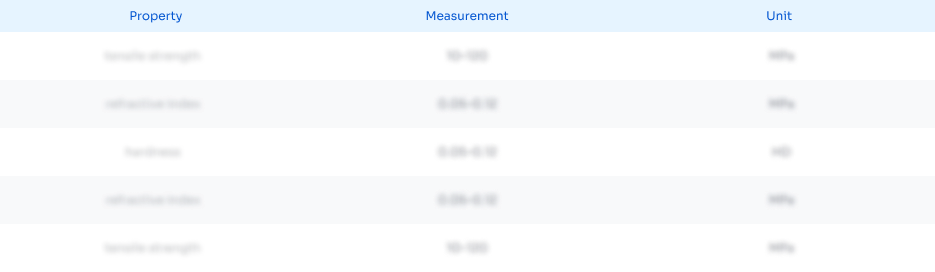
Abstract
Description
Claims
Application Information

- R&D
- Intellectual Property
- Life Sciences
- Materials
- Tech Scout
- Unparalleled Data Quality
- Higher Quality Content
- 60% Fewer Hallucinations
Browse by: Latest US Patents, China's latest patents, Technical Efficacy Thesaurus, Application Domain, Technology Topic, Popular Technical Reports.
© 2025 PatSnap. All rights reserved.Legal|Privacy policy|Modern Slavery Act Transparency Statement|Sitemap|About US| Contact US: help@patsnap.com