Fly ash-coal cinder cementing material and preparation method thereof
A technology of cementitious materials and fly ash, which is applied in the field of materials, can solve the problem of low utilization rate of slag and achieve the effect of strong coagulation
- Summary
- Abstract
- Description
- Claims
- Application Information
AI Technical Summary
Problems solved by technology
Method used
Image
Examples
Embodiment 1
[0037] A preparation method of fly ash-coal cinder cementitious material, it comprises the steps:
[0038] S1. Mix and stir fly ash, cinder, magnesium phosphate cement and retarder for 1-5 minutes, and stir evenly to form a mixture; retarder is borax. Wherein, based on the total weight of the mixture, the weight percentages of fly ash, coal cinder, cement and retarder are: magnesium phosphate cement dosage 19%, retarder dosage 1%, flyash dosage 60% and coal cinder Dosage 20%.
[0039] S2. Methyl methacrylate, sodium dodecylbenzenesulfonate and water are mixed to make an aqueous emulsion;
[0040] S3. Mix and stir the water emulsion of S2 and the mixture of S1 at a weight ratio of 0.18:1 to make a slurry of fly ash-cinder cementitious material. Wherein, based on the total weight of the aqueous emulsion, methyl methacrylate consumption 35wt%, sodium dodecylbenzenesulfonate 35wt% and water consumption 30wt.
Embodiment 2
[0042] With reference to embodiment 1, different from embodiment 1, on the basis of embodiment 1, also includes:
[0043] S4. The slurry of S3 is injected into the mould, then vibrated, left to form, demolded, then sealed and cured for 24-72h, and finally placed naturally to obtain solidified fly ash-cinder cementitious material.
Embodiment 3
[0044] The influence of embodiment 3 fly ash consumption on fluidity
[0045] With reference to Example 1, the influence of the amount of fly ash to the performance change of the fly ash-coal cinder cementitious material is tested by the univariate control method. The following table 3 shows that the amount of fly ash varies from 40% to 80% gradient, and other amounts are fixed.
[0046] The test method for the fluidity of the gelled material is as follows:
[0047] The test method of fluidity is carried out according to GB / T 2419-2005 "Measurement Method of Fluidity of Cement Mortar Sand" [, test equipment and parameters: the metal truncated cone circular mold with the cylinder size of 36mm×60mm×60mm is used, and the cone is placed in the center of the glass and wipe clean with a damp cloth. Take a certain amount of sample and conduct the test according to the standard method. In order to reduce the test error and improve the accuracy of the test, start timing when the coni...
PUM
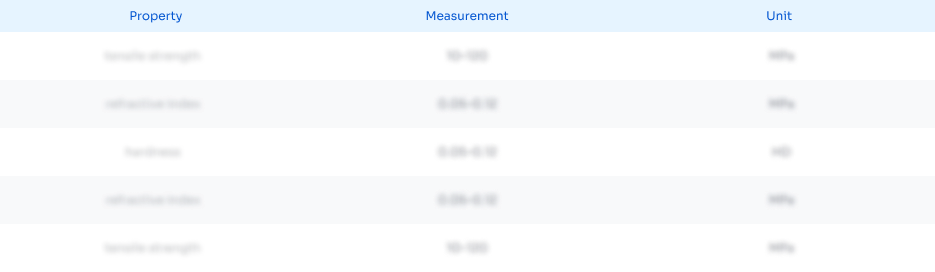
Abstract
Description
Claims
Application Information

- Generate Ideas
- Intellectual Property
- Life Sciences
- Materials
- Tech Scout
- Unparalleled Data Quality
- Higher Quality Content
- 60% Fewer Hallucinations
Browse by: Latest US Patents, China's latest patents, Technical Efficacy Thesaurus, Application Domain, Technology Topic, Popular Technical Reports.
© 2025 PatSnap. All rights reserved.Legal|Privacy policy|Modern Slavery Act Transparency Statement|Sitemap|About US| Contact US: help@patsnap.com