Autonomous docking control method for sliding steering modular robot
A skid steering and control method technology, applied in two-dimensional position/course control, control/regulation system, non-electric variable control, etc., can solve problems such as making up for lateral errors, affecting slippage, and positioning system deviations. Achieve the effects of eliminating slippage deviation, eliminating lateral deviation, and small steering angle
- Summary
- Abstract
- Description
- Claims
- Application Information
AI Technical Summary
Problems solved by technology
Method used
Image
Examples
Embodiment Construction
[0097] The method of the present invention is used to slip the self-directed control of the modular robot, and the processes are figure 1 Indicated. Paste the QR code target on the female module, install a single-graphic camera on the male module, through the visual + cooperation target technology, by means of the camera to detect the position of the target to accurately estimate the relative position of the module to be docked, compensate The error of the positioning system.
[0098] Self-docking is achieved by visual + cooperative target guidance. Take the two-dimensional code image by the camera and solve the two-dimensional code with respect to the attitude quad number of the camera coordinate system.
[0099] Use θ ori X angle Describe the QR code gesture, use Z d Describe the QR code position. Three key variable geometrics figure 2 Indicated. figure 2 The middle coordinate system is the camera coordinate system. θ ori It is the angle of the two-dimensional code plane and the...
PUM
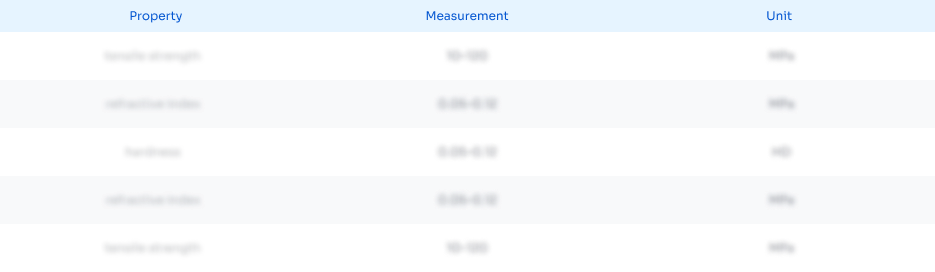
Abstract
Description
Claims
Application Information

- Generate Ideas
- Intellectual Property
- Life Sciences
- Materials
- Tech Scout
- Unparalleled Data Quality
- Higher Quality Content
- 60% Fewer Hallucinations
Browse by: Latest US Patents, China's latest patents, Technical Efficacy Thesaurus, Application Domain, Technology Topic, Popular Technical Reports.
© 2025 PatSnap. All rights reserved.Legal|Privacy policy|Modern Slavery Act Transparency Statement|Sitemap|About US| Contact US: help@patsnap.com