Bionic bamboo joint type soft actuator
An actuator and bionic bamboo technology, which is applied to passive exercise equipment, manipulators, program-controlled manipulators, etc., can solve the problems of the cavity of the soft actuator being easily collapsed, the overall stiffness is low, and the load capacity is low. Achieve the effect of improving compressive performance and tensile performance, good flexibility, and improving load capacity
- Summary
- Abstract
- Description
- Claims
- Application Information
AI Technical Summary
Problems solved by technology
Method used
Image
Examples
Embodiment 1
[0048] figure 1 and figure 2 The semi-sectional view of the bionic bamboo-type soft actuator and the radial sectional view of the radially symmetrical section of the peak passing module 1 are shown respectively.
[0049] see figure 1 and figure 2 , the bionic bamboo-style soft actuator includes an actuator body and an interface 6 . The actuator body includes several peak modules 1, several wave trough modules 2 and a drive cavity 7; one end of the actuator body is provided with the interface 6, and the other end is sealed, and the drive cavity 7 is arranged along the The axial distribution of the actuator body, the interface 6 communicates with the drive cavity 7, and external equipment can inject fluid into the drive cavity 7 through the interface 6 (can be but not limited to gas, water, hydraulic oil, etc.) to drive the bionic bamboo-style soft actuator to bend, and the interface 6 can be, for example, tubular structures such as cylindrical tubes, oval tubes, and squar...
Embodiment 2
[0070] image 3 and Figure 4a The semi-sectional view of the bionic bamboo-type soft actuator and the radial sectional view of the radially symmetrical section of the peak passing module 1 are shown respectively. Compared with Embodiment 1, the difference is that the inner circumferential ribs 3 of the inner slub rib module in this embodiment are arranged along the inner circumferential contour of the wave crest module 1, and other structures are basically the same, so the description will not be repeated.
[0071] see image 3 and Figure 4a , in this embodiment, the number of inner circumferential ribs 3 in the inner bamboo rib module is the same as the number of wave crest modules 1 of the bionic bamboo-type soft actuator, that is, the inner circumference There is a one-to-one correspondence relationship between the ribs 3 and the wave crest modules 1 , and each of the wave crest modules 1 is provided with an inner circumferential rib 3 on the circumferential inner contou...
Embodiment 3
[0078] Figure 5 and Figure 6 The semi-sectional view of the bionic bamboo-type soft actuator and the radial sectional view of the radially symmetrical section of the peak passing module 1 are shown respectively. Compared with Embodiment 1, the difference is that the inner circumferential ribs 3 of the inner slub rib module in this embodiment cover part of the circumferential inner contour of the valley module 2, and other structures are basically the same, so the description will not be repeated.
[0079] see Figure 5 and Figure 6 , the inner circumferential ribs 3 are in contact with the top surface and the bottom surface of the drive cavity 7 at the wave valley module 2 respectively, and the inner circumferential ribs 3 are in contact with the drive cavity at the wave valley module 2 The left and right sides of the body 7 do not touch. Of course, in some embodiments, the inner circumferential rib 3 is in contact with the left and right side surfaces of the driving ca...
PUM
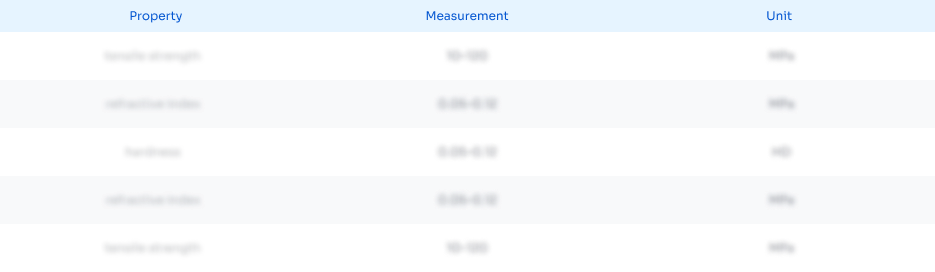
Abstract
Description
Claims
Application Information

- R&D Engineer
- R&D Manager
- IP Professional
- Industry Leading Data Capabilities
- Powerful AI technology
- Patent DNA Extraction
Browse by: Latest US Patents, China's latest patents, Technical Efficacy Thesaurus, Application Domain, Technology Topic, Popular Technical Reports.
© 2024 PatSnap. All rights reserved.Legal|Privacy policy|Modern Slavery Act Transparency Statement|Sitemap|About US| Contact US: help@patsnap.com