Control method for four-degree-of-freedom mechanical arm, and control method for fire-fighting mechanical arm of transformer substation
A control method and manipulator technology, applied in the direction of manipulators, comprehensive factory control, program control manipulators, etc., can solve the problems of low operating efficiency, low control accuracy, and inaccurate fixed-point positioning of manipulators in substation fire protection systems. Kinematics high-precision control problems, avoiding matrix operations, and high reliability effects
- Summary
- Abstract
- Description
- Claims
- Application Information
AI Technical Summary
Problems solved by technology
Method used
Image
Examples
Embodiment Construction
[0050] Such as figure 1 Shown is a schematic flow chart of the four-degree-of-freedom mechanical arm control method of the present invention: the four-degree-of-freedom mechanical arm control method provided by the present invention includes the following steps:
[0051] S1. Obtain the working parameters of the four-degree-of-freedom robotic arm;
[0052] S2. According to the position of the four-degree-of-freedom manipulator, establish a coordinate system; specifically, establish a Cartesian Cartesian coordinate system OXYZ on the plane where the four-degree-of-freedom manipulator is installed, where the plane on which the four-degree-of-freedom manipulator is installed is the OXY plane , the Z axis is perpendicular to the OXY plane and is collinear with the steering gear rotation axis of the first joint closest to the OXY plane of the four-degree-of-freedom manipulator; Tie;
[0053] S3. Obtain the target position information as the position information of the end of the m...
PUM
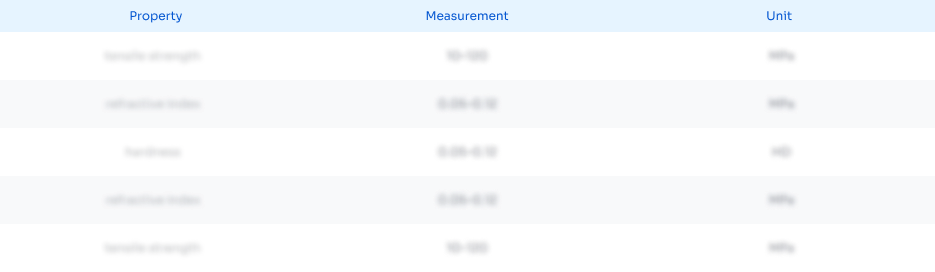
Abstract
Description
Claims
Application Information

- R&D Engineer
- R&D Manager
- IP Professional
- Industry Leading Data Capabilities
- Powerful AI technology
- Patent DNA Extraction
Browse by: Latest US Patents, China's latest patents, Technical Efficacy Thesaurus, Application Domain, Technology Topic, Popular Technical Reports.
© 2024 PatSnap. All rights reserved.Legal|Privacy policy|Modern Slavery Act Transparency Statement|Sitemap|About US| Contact US: help@patsnap.com