A Method for Determining Repair Welding Position
A determination method and repair welding technology, applied in welding equipment, measuring devices, auxiliary devices, etc., can solve the problems of inaccurate welding position data, inability to guarantee repair welding position accuracy, low work efficiency, etc., and achieve high accuracy. , High work efficiency, the effect of eliminating relative errors
- Summary
- Abstract
- Description
- Claims
- Application Information
AI Technical Summary
Problems solved by technology
Method used
Image
Examples
Embodiment 1
[0031] as attached figure 1 As shown, a method for determining a repair welding position includes the following steps:
[0032] Step 1: Fix the fiber to be tested. In this embodiment, a three-jaw chuck is used to clamp and fix the optical fiber to be tested, and the three-jaw chuck can vertically fix the optical fiber to be tested, which is convenient for rotating the optical fiber to be tested in the subsequent process.
[0033] Step 2: Adjust the up and down displacement of the optical fiber to be tested, so that the detection part of the optical fiber to be tested is aligned with the detection device and the repair welding device; it is convenient for the detection of the detection device and the repair welding of the repair welding device.
[0034] In this embodiment, the detection device is a conventional optical power meter, and the detection part of the optical fiber to be tested is aligned with the detection head of the optical power meter.
[0035] Step 3: Drive the...
Embodiment 2
[0041] A method for determining a repair welding position, comprising the following steps:
[0042] Step 1: Fix the fiber to be tested;
[0043]The optical fiber to be tested in this embodiment is an optical fiber connected to the connector, and the connection method between the connector and the optical fiber is welding; the welding position between the connector and the optical fiber is the position to be detected of the optical fiber to be tested; connection to the fiber. In practical applications, the connection between optical fibers and the connection between optical fibers and other components require connectors to achieve the connection effect, and the tightness of the connection between the connector and the optical fiber will affect the working performance of the optical fiber. Set the welding position as the part to be detected , the welding status can be determined through the detection device in the subsequent steps, and the defects can be remedied in time to avo...
PUM
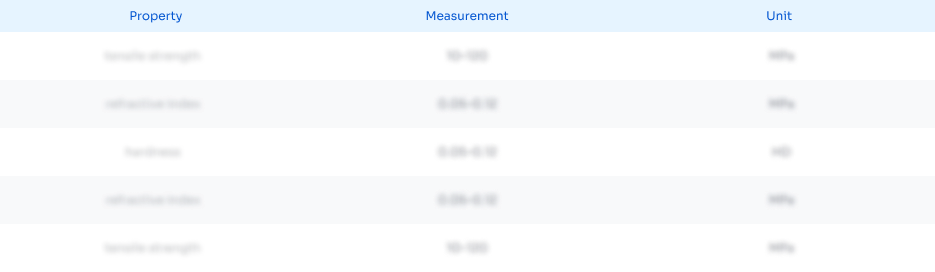
Abstract
Description
Claims
Application Information

- R&D
- Intellectual Property
- Life Sciences
- Materials
- Tech Scout
- Unparalleled Data Quality
- Higher Quality Content
- 60% Fewer Hallucinations
Browse by: Latest US Patents, China's latest patents, Technical Efficacy Thesaurus, Application Domain, Technology Topic, Popular Technical Reports.
© 2025 PatSnap. All rights reserved.Legal|Privacy policy|Modern Slavery Act Transparency Statement|Sitemap|About US| Contact US: help@patsnap.com