Pipeline measurement system pose calibration method for point cloud splicing
A measurement system and pose calibration technology, which is applied in image data processing, instruments, calculations, etc., can solve problems such as inability to extract enough feature points, incapable of turntable pose calibration, etc., and achieve the effect of improving accuracy
- Summary
- Abstract
- Description
- Claims
- Application Information
AI Technical Summary
Problems solved by technology
Method used
Image
Examples
Embodiment Construction
[0034] A preferred embodiment of the present invention will be described below with reference to the drawings. It is to be understood that the preferred embodiments described herein are intended to illustrate and explain the invention and are not intended to limit the invention.
[0035] The present invention discloses a pipe measuring system bit postage method for point cloud splicing, such as figure 1 As shown, including the following steps:
[0036] S1, establish a mathematical model of coordinate conversion of pipeline measurement systems;
[0037] S2, use the pipeline measurement system to measure the entire ring fixed inner diameter cylinder in advance, generate different angles of camera coordinate interior surface points cloud;
[0038] S3, change the camera coordinate system to the point cloud cylindrical coordinate system by cylindrical fitting.
[0039] S4, seeking point clouds under the same angle in the global cylindrical coordinate system, that is, solicited point cl...
PUM
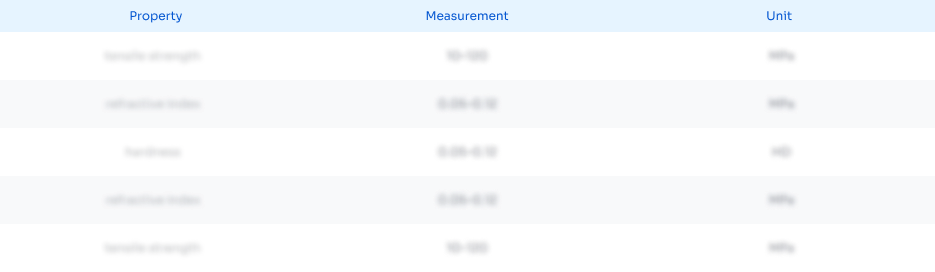
Abstract
Description
Claims
Application Information

- R&D
- Intellectual Property
- Life Sciences
- Materials
- Tech Scout
- Unparalleled Data Quality
- Higher Quality Content
- 60% Fewer Hallucinations
Browse by: Latest US Patents, China's latest patents, Technical Efficacy Thesaurus, Application Domain, Technology Topic, Popular Technical Reports.
© 2025 PatSnap. All rights reserved.Legal|Privacy policy|Modern Slavery Act Transparency Statement|Sitemap|About US| Contact US: help@patsnap.com