Front edge bending test tool and method
A bending test and leading edge technology, applied in the field of aircraft structure, can solve problems such as poor versatility, inconsistent with real working conditions, and unintuitive test results
- Summary
- Abstract
- Description
- Claims
- Application Information
AI Technical Summary
Problems solved by technology
Method used
Image
Examples
Embodiment
[0090] 1. The design method of the leading edge bending test tooling, the steps are as follows:
[0091] 1) Determine the shape of the ribbed plate 10 according to the cross-sectional shape of the front edge. When the front edge is a structure with a gradual change in cross-section, the shapes of the two ribbed plates 10 can be different;
[0092] 2) Determine the distance of the riser according to the length of the leading edge;
[0093] 3) According to the deformation requirements, determine the size and relative position of the long rotating rod and the short rotating rod through the calculation of the schematic diagram;
[0094] 4) Determine the torque wrench to be selected according to the size of the load, and determine the size of the hexagonal side of the loading end 7 according to the specifications of the torque wrench socket, and determine the size of the square side of the loading end 7 according to the size of the short rotating rod. It is also possible to make m...
PUM
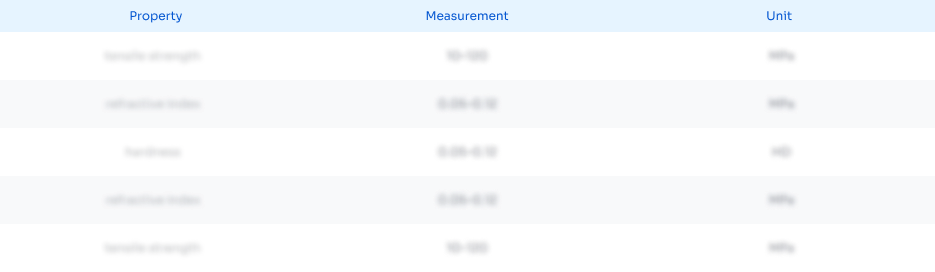
Abstract
Description
Claims
Application Information

- R&D
- Intellectual Property
- Life Sciences
- Materials
- Tech Scout
- Unparalleled Data Quality
- Higher Quality Content
- 60% Fewer Hallucinations
Browse by: Latest US Patents, China's latest patents, Technical Efficacy Thesaurus, Application Domain, Technology Topic, Popular Technical Reports.
© 2025 PatSnap. All rights reserved.Legal|Privacy policy|Modern Slavery Act Transparency Statement|Sitemap|About US| Contact US: help@patsnap.com