Ultrasonic automatic detection device and cable internal damage detection method
An automatic detection device, ultrasonic detection technology, applied in measuring devices, using ultrasonic/sonic/infrasonic waves, using sound waves/ultrasonic/infrasonic waves to analyze solids, etc. Problems such as high manual operation intensity can achieve the effect of strong load capacity, reduced moving speed and high driving efficiency
- Summary
- Abstract
- Description
- Claims
- Application Information
AI Technical Summary
Problems solved by technology
Method used
Image
Examples
Embodiment 1
[0034] like figure 1 As shown, an ultrasonic automatic detection device includes an ultrasonic detection module 1 , a rotary base 2 and a mechanical arm moving device 3 . The rotary base 2 is installed on the fixed platform. The moving device 3 of the mechanical arm is installed on the rotary base 2 . The ultrasonic detection module 1 is installed at the end of the mechanical arm moving device 3 .
[0035] like figure 2 As shown, the slewing base 2 includes an upper support plate 2.1, a ball 2.2, a steering support rod 2.3, a rotating steering gear 2.4 and a lower support plate 2.5. The lower support plate 2.5 is fixed on the fixed platform. The rotary steering gear 2.4 is fixed on the center position of the lower support plate 2.5 top surface. The lower support plate 2.5 is fixed with five steering support rods 2.3 vertically arranged and evenly distributed along the circumferential direction of the axis of the lower support plate 2.5. The top of the steering support r...
Embodiment 2
[0048] The difference between this embodiment and Embodiment 1 is that the present invention can be applied to the non-destructive testing of other flexible structures, and the ultrasonic transceiver 1.7 can be replaced according to the change of the outer contour of the object to be tested, so that the probe of the ultrasonic transceiver 1.7 can be more fitted to the measured object Flexible structured surface.
PUM
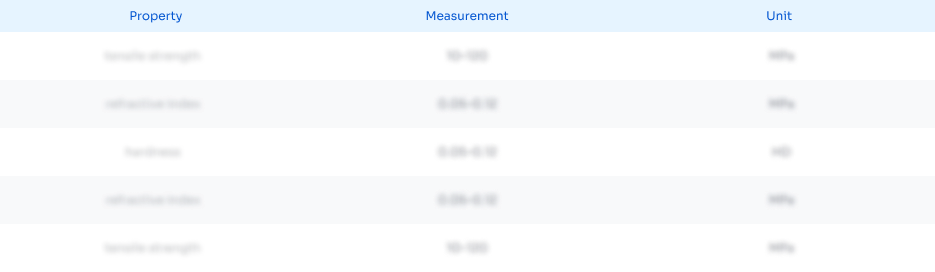
Abstract
Description
Claims
Application Information

- R&D
- Intellectual Property
- Life Sciences
- Materials
- Tech Scout
- Unparalleled Data Quality
- Higher Quality Content
- 60% Fewer Hallucinations
Browse by: Latest US Patents, China's latest patents, Technical Efficacy Thesaurus, Application Domain, Technology Topic, Popular Technical Reports.
© 2025 PatSnap. All rights reserved.Legal|Privacy policy|Modern Slavery Act Transparency Statement|Sitemap|About US| Contact US: help@patsnap.com