Automobile lamp mounting foot structure
A technology for automotive lamps and mounting feet, which is applied in signal devices, vehicle parts, transportation and packaging, etc., which can solve the problems of long adjustment period, failure to adjust qualified, large deformation of shell injection molding, etc.
- Summary
- Abstract
- Description
- Claims
- Application Information
AI Technical Summary
Problems solved by technology
Method used
Image
Examples
Embodiment Construction
[0014] Combine below Figure 1-Figure 8 The present invention is discussed in further detail.
[0015] An automobile lamp mounting foot structure, comprising a lamp housing 10, a mounting foot 20 is provided at the connection position between the lamp housing 10 and the vehicle body sheet metal A, the mounting foot 20 forms a detachable connection with the lamp housing 10, and the mounting foot 20 A threaded hole 21 is opened on the top, and the bolt 30 passes through the threaded hole 21 to fix the mounting foot 20 and the body sheet A. The mounting foot 20 and the lamp housing 10 are made into separate parts, and injection molding is carried out independently. The process is simple, and the deformation of the two parts is small, thereby ensuring the clearance between the lamp and the body sheet metal and the surrounding fittings. Even if the deformation of the lamp housing is relatively large, the mounting feet 20 can be adjusted to achieve adjustment, installation and matc...
PUM
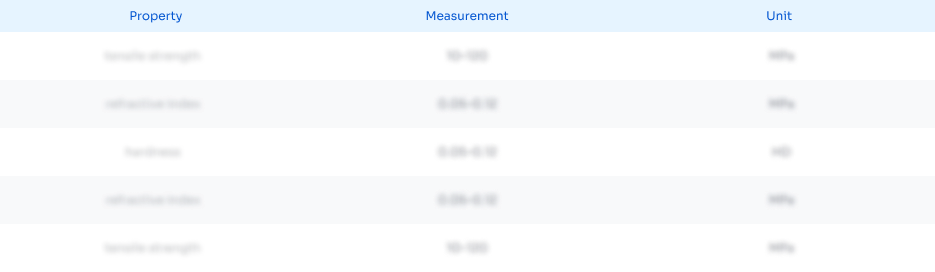
Abstract
Description
Claims
Application Information

- Generate Ideas
- Intellectual Property
- Life Sciences
- Materials
- Tech Scout
- Unparalleled Data Quality
- Higher Quality Content
- 60% Fewer Hallucinations
Browse by: Latest US Patents, China's latest patents, Technical Efficacy Thesaurus, Application Domain, Technology Topic, Popular Technical Reports.
© 2025 PatSnap. All rights reserved.Legal|Privacy policy|Modern Slavery Act Transparency Statement|Sitemap|About US| Contact US: help@patsnap.com