A closed-loop dynamic matrix control method for continuous stirring reactor
A stirring reactor and closed-loop dynamic technology, which is applied in the direction of electric controllers and controllers with specific characteristics, can solve problems such as unreachable dynamic characteristics, and achieve the effects of improving closed-loop dynamics, suppressing reverse response, and simple parameter adjustment
- Summary
- Abstract
- Description
- Claims
- Application Information
AI Technical Summary
Problems solved by technology
Method used
Image
Examples
specific Embodiment approach
[0052] Step 2, calculate the feed-forward response model offline. Its specific implementation is as follows:
[0053] Step 2-1, firstly determine the desired closed-loop response model, which is set as a step process in this example so as to demonstrate the closed-loop tracking characteristics of the present invention.
[0054] Step 2-2, Solve the optimization problem
[0055]
[0056] s.t.
[0057]
[0058]
[0059] in Represents the feed-forward response model that needs to be optimized, Σ represents the summation, Indicates the jth parameter of the step response model of the process object, Indicates the i-th parameter of the expected closed-loop response model, N m Indicates the model length, which is set to 21 in this example, and β indicates the stability coefficient, which is set to 0.05 in this example.
[0060] Step 2-3, according to the feed-forward response model obtained in step 2-2, determine the actual closed-loop response model in, Indicates ...
PUM
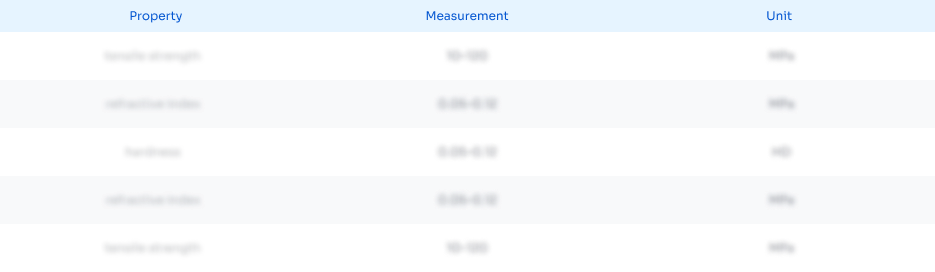
Abstract
Description
Claims
Application Information

- Generate Ideas
- Intellectual Property
- Life Sciences
- Materials
- Tech Scout
- Unparalleled Data Quality
- Higher Quality Content
- 60% Fewer Hallucinations
Browse by: Latest US Patents, China's latest patents, Technical Efficacy Thesaurus, Application Domain, Technology Topic, Popular Technical Reports.
© 2025 PatSnap. All rights reserved.Legal|Privacy policy|Modern Slavery Act Transparency Statement|Sitemap|About US| Contact US: help@patsnap.com