Flight equipment lift force testing device, system and method
A technology of flight equipment and test device, applied in the fields of aviation and mechanics measurement, which can solve problems such as unreliability and inaccurate lift test
- Summary
- Abstract
- Description
- Claims
- Application Information
AI Technical Summary
Problems solved by technology
Method used
Image
Examples
Embodiment 1
[0058] Such as figure 1 Shown: a flight equipment lift test device 1, comprising:
[0059] A tension measuring component 11, which is flexibly connected to the flying device 3, is used to measure the data that the flying device 3 produces on the pulling force measuring component 11 in a flying state for characterizing the pulling force;
[0060] An angle measurement part 12, which is connected with the tension measurement part 11, is used to measure the data used to characterize the tension angle of the flying device 3 in the flight state, and the tension angle is that the tension measurement part 11 is subjected to the The angle between the pulling force direction of the flying device 3 and the measuring reference plane of the angle measuring component 12;
[0061] The attitude measuring component 13 is arranged on the flying device 3 and is used to measure the data representing the roll angle of the flying device 3 in a flying state.
[0062] The working principle of this ...
Embodiment 2
[0117] Such as Figure 4 As shown, a flight equipment lift test method, using the flight equipment lift test system 2, realizes the test of the lift produced by the flight equipment 3 in the flight state, including:
[0118] S100: Adjust the horizontal adjustment component to make the installation base 14 parallel to the horizontal plane, initialize the tension measurement component 11, the angle measurement component 12 and the attitude measurement component 13, and obtain the weight of the flying device 3.
[0119] In this step, a level is installed on the level adjustment part, and the level adjustment part is adjusted to make the level reach a level state, thereby ensuring the accuracy of the lift test;
[0120] By initializing the tension measurement component 11 to make the tension value zero, avoid the interference of the data of the previous test on this test;
[0121] By initializing the angle measuring part 12, the deflection angle of the rotating part 123 is zero, ...
Embodiment 3
[0132] Such as Figure 5 Shown, a kind of flight equipment lift test device 1 comprises:
[0133] A tension measuring component 11, which is flexibly connected to the flying device 3, is used to measure the data that the flying device 3 produces on the pulling force measuring component 11 in a flying state for characterizing the pulling force;
[0134] An angle measurement part 12, which is connected with the tension measurement part 11, is used to measure the data used to characterize the tension angle of the flying device 3 in the flight state, and the tension angle is that the tension measurement part 11 is subjected to the The angle between the pulling force direction of the flying device 3 and the measuring reference plane of the angle measuring component 12;
[0135] The attitude measuring component 13 is arranged on the flying device 3 and is used to measure the data representing the roll angle and the pitch angle of the flying device 3 in the flying state.
[0136] The...
PUM
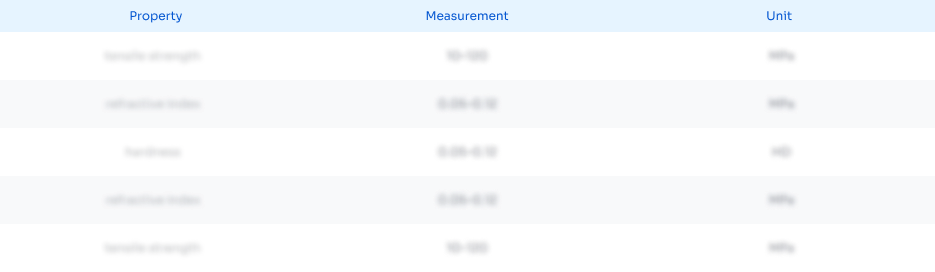
Abstract
Description
Claims
Application Information

- R&D Engineer
- R&D Manager
- IP Professional
- Industry Leading Data Capabilities
- Powerful AI technology
- Patent DNA Extraction
Browse by: Latest US Patents, China's latest patents, Technical Efficacy Thesaurus, Application Domain, Technology Topic, Popular Technical Reports.
© 2024 PatSnap. All rights reserved.Legal|Privacy policy|Modern Slavery Act Transparency Statement|Sitemap|About US| Contact US: help@patsnap.com