Transcritical main shaft system design method based on multi-scale interface regulation and control
A technology of interface control and system design, applied in the direction of geometric CAD, special data processing applications, etc., can solve problems such as the limitation of spindle parameters, the increase of spindle amplitude, and the friction accident of bearing rotors, so as to improve the bearing capacity and stiffness, and improve the dynamic performance. Stability, improve the effect of dynamic pressure effect
- Summary
- Abstract
- Description
- Claims
- Application Information
AI Technical Summary
Problems solved by technology
Method used
Image
Examples
Embodiment Construction
[0053] In order to ensure the stability of the spindle system, the design of the conventional high-speed hydrodynamic spindle system must strictly limit a series of parameters such as the stiffness, mass, span, and structure of the spindle, so that the design speed is lower than the critical speed. However, when the parameters of the spindle are limited and the operating speed of the spindle is higher than the critical speed, the traditional design method of the spindle system is no longer applicable.
[0054] In order to solve the above problems, the present invention ensures the safety and stability of the spindle system under critical speed conditions by rationally designing the multi-scale interface of the bearing, and proposes a design method for a transcritical spindle system based on multi-scale interface regulation. Transcritical spindle system, a transcritical spindle system is a spindle system that can work normally across critical speeds, and the multi-scale interfac...
PUM
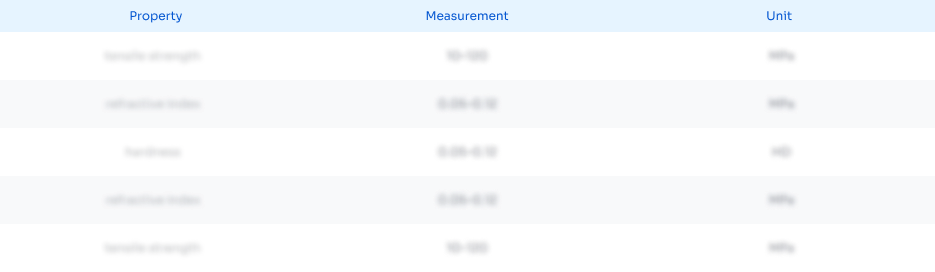
Abstract
Description
Claims
Application Information

- Generate Ideas
- Intellectual Property
- Life Sciences
- Materials
- Tech Scout
- Unparalleled Data Quality
- Higher Quality Content
- 60% Fewer Hallucinations
Browse by: Latest US Patents, China's latest patents, Technical Efficacy Thesaurus, Application Domain, Technology Topic, Popular Technical Reports.
© 2025 PatSnap. All rights reserved.Legal|Privacy policy|Modern Slavery Act Transparency Statement|Sitemap|About US| Contact US: help@patsnap.com