Mixing device for mixing catalyst carrier raw materials, and mixing method thereof
A catalyst carrier and mixing device technology, applied in mixing methods, chemical instruments and methods, mixers with rotary stirring devices, etc., can solve the problems of easy agglomeration, harsh on-site environment, high labor intensity, etc. , high production efficiency, airtight and uniform mixing effect
- Summary
- Abstract
- Description
- Claims
- Application Information
AI Technical Summary
Problems solved by technology
Method used
Image
Examples
Embodiment 1
[0065] use figure 1 with figure 2 The devices shown are mixed with a catalyst carrier feedstock. The apparatus includes: from the upper cover 11, the lower cover 13 is surrounded by a mixing chamber 1; the agitation unit 2 includes a spindle 21, three connecting shafts 22, and three stirring paddle 23, the spindle 21 Through the central portion of the upper cover 11 is connected to the three connecting shafts 22, three connecting pads 22 are provided with a stirring paddle 23, respectively, and three stirring paddle 23 in three connecting 22 ends. The frame mixing paddler as a mixed blade 231 is respectively, and the double-paddle mixing paddle of the dispersion blade 232 is a blade-shaped stirring paddle as a scraper blade 233, and a stirring paddle is provided at the end of the connecting shaft 22 23 Uniformly distributed along the circumference; the drive mechanism 6 for driving the stirring unit 2 is coupled to the spindle 21 of the stirring unit 2 (specifically a motor in thi...
Embodiment 2
[0071] According to the method of Example 1, in different, in step 1), the dry mixing time was 20 min, and the stirring speed was 200R / min; step 2), the dry mixture was 10 min, and the stirring velocity was 300 r / min. Also, the automatic, sealed and uniform mixing of the catalyst carrier feedstock can be realized by the mixing apparatus provided by the present invention and the mixing method. Further, by adopting a mixing apparatus provided by the present invention and the above-described mixing method, a high production efficiency, a carrier mixture has no agglomeration, and is easy to achieve continuous production of the catalyst carrier.
Embodiment 3
[0073] According to the method of Example 1, in different, in step 1), the dry mixing time was 25 min, and the stirring speed was 180 r / min; step 2), the dry mixture was 30 min, and the stirring speed was 80 r / min. Also, the automatic, sealed and uniform mixing of the catalyst carrier feedstock can be realized by the mixing apparatus provided by the present invention and the mixing method. Further, by adopting a mixing apparatus provided by the present invention and the above-described mixing method, a high production efficiency, a carrier mixture has no agglomeration, and is easy to achieve continuous production of the catalyst carrier.
PUM
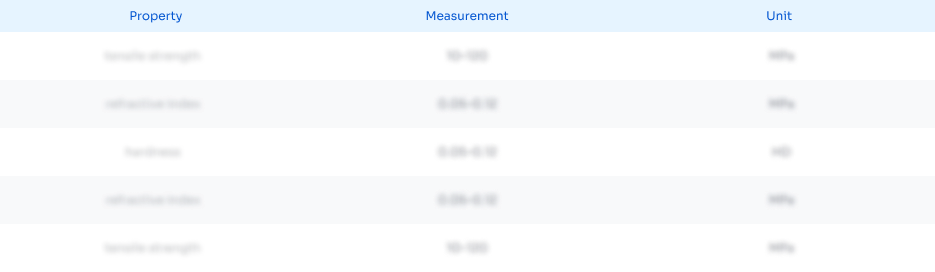
Abstract
Description
Claims
Application Information

- R&D
- Intellectual Property
- Life Sciences
- Materials
- Tech Scout
- Unparalleled Data Quality
- Higher Quality Content
- 60% Fewer Hallucinations
Browse by: Latest US Patents, China's latest patents, Technical Efficacy Thesaurus, Application Domain, Technology Topic, Popular Technical Reports.
© 2025 PatSnap. All rights reserved.Legal|Privacy policy|Modern Slavery Act Transparency Statement|Sitemap|About US| Contact US: help@patsnap.com