Intelligent conducting wire shockproof damper
A technology of anti-vibration hammer and wire, used in photovoltaic power generation, photovoltaic modules, electrical components and other directions
- Summary
- Abstract
- Description
- Claims
- Application Information
AI Technical Summary
Problems solved by technology
Method used
Image
Examples
Embodiment 1
[0041] The present application examples disclose a smart lead shock hammer, reference figure 1, Includes the main control unit for detecting the wire vibration frequency and the amplitude and output signal, the main control unit includes the vibration detecting element 51, the vibration detecting element 51 is a vibration sensor, and the vibration sensor consists of strain sheet and strain beam for detecting the wire. Vibration frequency and vibration amplitude. The vibration detecting element 51 outputs the microcontroller 57, the microcontroller 57 is the MCU, and the output signal of the vibration detecting element 51 is used to measure, calculate the vibration frequency and vibration amplitude of the wire. The microcontroller 57 output is electrically connected to the motor drive unit 54, and the motor drive unit 54 outputs the mechanical vibration tuning unit 55. The motor drive unit 54 accepts the command of the microcontroller 57 to drive the mechanical vibration tuning uni...
Embodiment 2
[0052] In the present application, the second disclosure of an intelligent wire shock hammer, reference Figure 6 Different from the embodiment, the two damping elastic rods 3 are in the same vertical surface and the resonance frequency adjustment nut 41 is horizontally, and the resonant frequency adjustment nut 41 of the same piece is connected to the screw 42 and damping elasticity of the nut 41. The rod 3 is in the same horizontal plane, and the two screws 42 are also located in the same vertical plane, the screw gear 43 and the fixed end 22 in the same horizontal plane, the resonant frequency adjustment nut 41 in the position of the damping elastic rod 3 is slidably connected to The internal bottom surface of the outer casing B 31, the resonant frequency adjustment nut 41 in the position of the housing mozzare, the resonance frequency adjustment nut 4 is slidably connected to the inner top surface of the outer casing B 31, and the outer mold is integrally formed with a vertical...
Embodiment 3
[0055] The third disclosure of the present application discloses an intelligent wire shock hammer, reference Figure 7 with Figure 8 In the case of the first embodiment, the second embodiment is the same, the two damping elastic rods 3 are the same, and the outer casing moral bracket is integrally formed with a vertical bracket 24, and the bracket 24 is parallel to the outer casing B 31 width direction, damped elastic rod. The fixed end 22 of the 3 is located at the two opposing vertical side surfaces of the bracket 24, and the resonant frequency adjustment nut 41 is vertically, the resonant frequency adjustment nut 41 is slide to be connected to the bottom surface of the outer casing B 31, and the two screws 42 are rotatably connected to the bracket 24, respectively. The two screw 42 axis is the same relative to the two vertical side, and the screw 42 is located directly above the damping elastic rod 3, and the two screw gear 43 are adjacent to the bracket 24, and the drive rod 44...
PUM
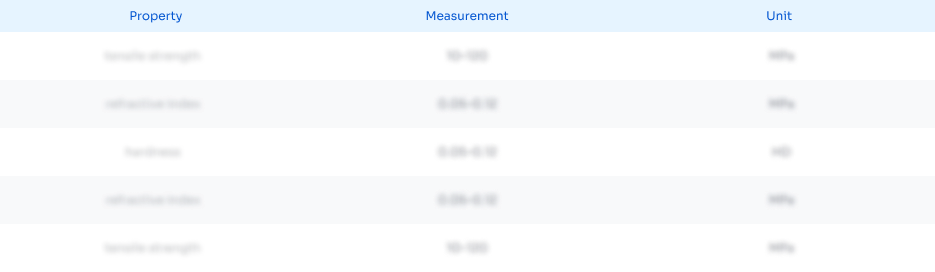
Abstract
Description
Claims
Application Information

- R&D
- Intellectual Property
- Life Sciences
- Materials
- Tech Scout
- Unparalleled Data Quality
- Higher Quality Content
- 60% Fewer Hallucinations
Browse by: Latest US Patents, China's latest patents, Technical Efficacy Thesaurus, Application Domain, Technology Topic, Popular Technical Reports.
© 2025 PatSnap. All rights reserved.Legal|Privacy policy|Modern Slavery Act Transparency Statement|Sitemap|About US| Contact US: help@patsnap.com