Cooling system device for magnetic axial bearing
An axial bearing and cooling system technology, applied in the direction of bearing cooling, magnetic bearing, shaft and bearing, etc., can solve the problems of increasing friction, reducing system reliability, poor ventilation and heat dissipation conditions, and achieving the effect of uniform heat dissipation
- Summary
- Abstract
- Description
- Claims
- Application Information
AI Technical Summary
Problems solved by technology
Method used
Image
Examples
Embodiment Construction
[0028] In order to facilitate understanding of the present invention, the present invention will be described more fully described with reference to the related drawings. The preferred embodiment of the present invention is given in the drawings. However, the present invention can be implemented in a variety of different forms, and is not limited to the embodiments described herein. Conversely, the purpose of providing these embodiments is to make a more thorough understanding of the disclosure of the present invention.
[0029] Further, the elements in the present invention are referred to as "fixed to" or "set to" another element, which can be directly in another element or may also exist in the hidden components. When a component is considered to be "connected" another element, it may be directly connected to another element or may always exist in the center element. The term "vertical", "horizontal", "left", "right", "left", "right", "left", "right", and similar expressions ar...
PUM
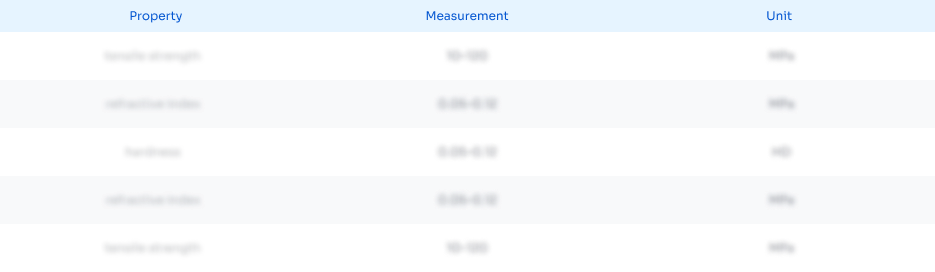
Abstract
Description
Claims
Application Information

- R&D
- Intellectual Property
- Life Sciences
- Materials
- Tech Scout
- Unparalleled Data Quality
- Higher Quality Content
- 60% Fewer Hallucinations
Browse by: Latest US Patents, China's latest patents, Technical Efficacy Thesaurus, Application Domain, Technology Topic, Popular Technical Reports.
© 2025 PatSnap. All rights reserved.Legal|Privacy policy|Modern Slavery Act Transparency Statement|Sitemap|About US| Contact US: help@patsnap.com