Parallel robot with four built-in rods and four degrees of freedom
A technology with a degree of freedom and a built-in rod, which is applied in the direction of manipulators, program-controlled manipulators, manufacturing tools, etc., can solve problems affecting load weight, etc., and achieve the effect of increasing load quality and enhancing rigidity
- Summary
- Abstract
- Description
- Claims
- Application Information
AI Technical Summary
Problems solved by technology
Method used
Image
Examples
Embodiment Construction
[0028] Three degrees of freedom parallel robot with four built-in rods, see Figure 2-Figure 8 : It includes a suspension frame 1, four sets of servo systems, four sets of transmission rod assemblies, and a linkage plate 11;
[0029] The suspension frame 1 is used for the hardware support of the overall structure, the suspension frame 1 is a square frame, and a group of servo systems are respectively fixed in the four intersection positions of the square frame;
[0030] Each set of servo system is used to transmit power, and the output end of the servo system is connected to the power arm 5 of the transmission rod assembly of the corresponding set;
[0031] Each set of transmission rod assemblies includes a first parallelogram transmission assembly a and a second parallelogram transmission assembly b. The first parallelogram transmission assembly a includes a power arm 5, a linkage arm 6, and an extension arm 9. The output end of the servo system is pivotally connected to the ...
PUM
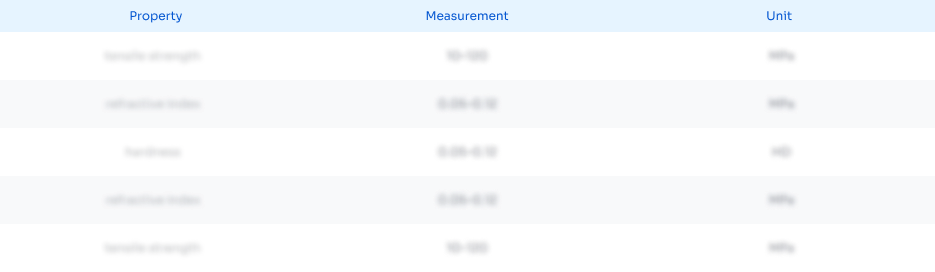
Abstract
Description
Claims
Application Information

- R&D Engineer
- R&D Manager
- IP Professional
- Industry Leading Data Capabilities
- Powerful AI technology
- Patent DNA Extraction
Browse by: Latest US Patents, China's latest patents, Technical Efficacy Thesaurus, Application Domain, Technology Topic, Popular Technical Reports.
© 2024 PatSnap. All rights reserved.Legal|Privacy policy|Modern Slavery Act Transparency Statement|Sitemap|About US| Contact US: help@patsnap.com