Oil sealing cover structure with thrust function
A technology of oil seal and function, applied in the field of oil seal structure, can solve the problem of low negative pressure resistance of the shaft system, achieve high installation accuracy, improve reliability, and simple structure
- Summary
- Abstract
- Description
- Claims
- Application Information
AI Technical Summary
Problems solved by technology
Method used
Image
Examples
Embodiment Construction
[0016] The preferred embodiments of the present invention will be described below in conjunction with the accompanying drawings. It should be understood that the preferred embodiments described here are only used to illustrate and explain the present invention, and are not intended to limit the present invention.
[0017] like Figure 1-Figure 4 As shown, an oil seal cover structure with a thrust effect includes a turbine rotor 1, a bearing body 2, an integral bearing sleeve 3 and an impeller 7, the integral bearing sleeve 3 is installed inside the bearing body 2, and the turbine The rotor 1 is installed in the inner hole of the integral bearing sleeve 3, the left and right ends of the turbine rotor 1 extend out of the bearing body 2, the impeller 7 is installed on the right side outside the turbine rotor 1, and the turbine rotor 1 is located outside the impeller A sealing sleeve 4 is installed between 7 and the integral bearing sleeve 3, and an oil sealing cover 5 is installe...
PUM
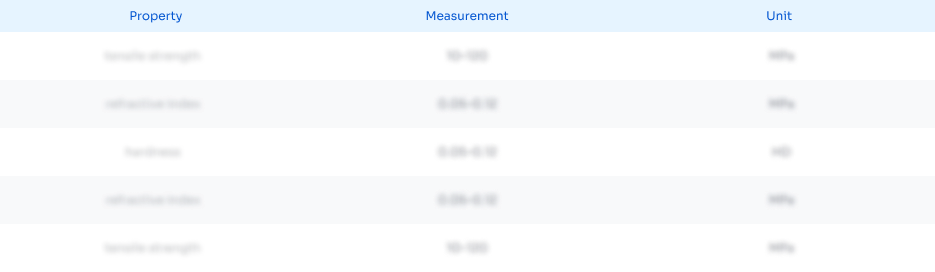
Abstract
Description
Claims
Application Information

- R&D Engineer
- R&D Manager
- IP Professional
- Industry Leading Data Capabilities
- Powerful AI technology
- Patent DNA Extraction
Browse by: Latest US Patents, China's latest patents, Technical Efficacy Thesaurus, Application Domain, Technology Topic, Popular Technical Reports.
© 2024 PatSnap. All rights reserved.Legal|Privacy policy|Modern Slavery Act Transparency Statement|Sitemap|About US| Contact US: help@patsnap.com