Brake and rotating device with brake
A technology of rotating device and brake rotor, applied in the direction of brake type, manufacturing tool, brake actuator, etc., can solve the problem of environmental pollution inside the module, and achieve the effect of not easy machine damage, fast action, and guaranteed temperature environment.
- Summary
- Abstract
- Description
- Claims
- Application Information
AI Technical Summary
Problems solved by technology
Method used
Image
Examples
Embodiment 1
[0038] This embodiment provides a specific implementation of the brake, such as figure 1 As shown, including: brake stator 1, brake plate 2 and brake rotor 3. Wherein, the brake rotor 3 is suitable for being fixedly connected with the rotating shaft 4 of the rotating device, specifically, the fixed connection can be made through the structure of fasteners and flanges, or can be fixedly connected through welding. The brake plate 2 can be slidably arranged on the brake stator 1 in the axial direction. Specifically, the brake stator 1 is provided with a guide column 5, and the other end of the guide column 5 is connected to a fixed disk 6 to make The moving plate 2 is slidably connected to the guide post 5 . The brake plate 2 is opposite to the brake rotor 3 and kept spaced, as Figure 4 As shown, the brake plate 2 has a notch 7 for accommodating the guide post 5 , and a plurality of guide posts 5 are snapped into the notch 7 to guide the brake plate 2 . The brake plate 2 also...
Embodiment 2
[0046] This embodiment provides a specific implementation of a rotating device, which can be used in a joint module of a collaborative robot.
[0047] Such as Image 6 As shown, the rotating device includes: a housing 14 having a shaft chamber 15 for installing the shaft 4 and a brake chamber 16 communicating with the shaft chamber 15 in the axial direction. A rotating shaft 4 is installed in the rotating shaft chamber 15, and one end of the rotating shaft 4 protrudes from the rotating shaft chamber 15 into the brake chamber 16; the brake described in Embodiment 1 is installed in the brake chamber 16, The rotating shaft 4 protrudes from the rotating shaft cavity 15 and is fixedly connected with the brake rotor 3 of the brake.
[0048] Specifically, the brake stator 1 of the brake is installed on the side of the brake cavity 16 close to the shaft cavity 15 by fasteners, and the brake stator 1 has a through hole 10, which is used for the shaft 4 through. Similarly, the brake ...
PUM
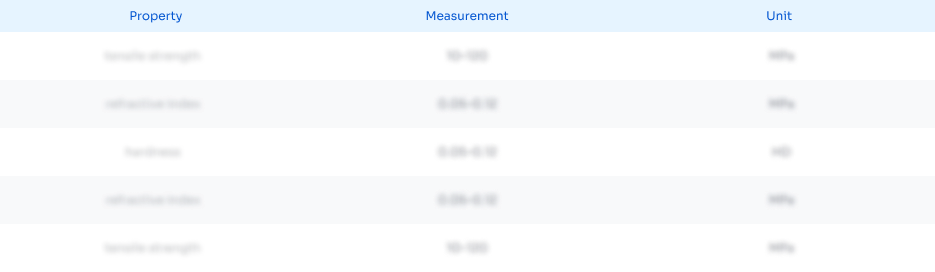
Abstract
Description
Claims
Application Information

- R&D
- Intellectual Property
- Life Sciences
- Materials
- Tech Scout
- Unparalleled Data Quality
- Higher Quality Content
- 60% Fewer Hallucinations
Browse by: Latest US Patents, China's latest patents, Technical Efficacy Thesaurus, Application Domain, Technology Topic, Popular Technical Reports.
© 2025 PatSnap. All rights reserved.Legal|Privacy policy|Modern Slavery Act Transparency Statement|Sitemap|About US| Contact US: help@patsnap.com