Robot gripper and control method thereof
A robot gripper and control part technology, applied in the field of robotics, can solve the problems of inability to limit the gripper, poor integration, and failure to provide, etc., and achieve the effects of improved integration, compact structure, and small size
- Summary
- Abstract
- Description
- Claims
- Application Information
AI Technical Summary
Problems solved by technology
Method used
Image
Examples
Embodiment Construction
[0038] In order to make the object, technical scheme and advantages of the present invention clearer, a specific embodiment in the present invention will be clearly and completely described below in conjunction with the accompanying drawings. Obviously, the described specific embodiment is an example of implementing the present invention , does not constitute a limitation to the scope of the present invention. Based on the implementation manners in the present invention, all other implementation manners obtained by persons of ordinary skill in the art without creative efforts fall within the protection scope of the present invention.
[0039] In addition, the term "and / or" in this article is only an association relationship describing associated objects, which means that there may be three relationships, for example, A and / or B, which may mean: A exists alone, A and B exist at the same time, There are three cases of B alone. In addition, the character " / " in this article gene...
PUM
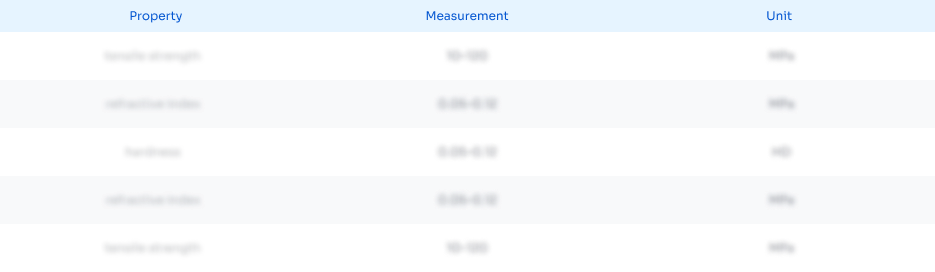
Abstract
Description
Claims
Application Information

- Generate Ideas
- Intellectual Property
- Life Sciences
- Materials
- Tech Scout
- Unparalleled Data Quality
- Higher Quality Content
- 60% Fewer Hallucinations
Browse by: Latest US Patents, China's latest patents, Technical Efficacy Thesaurus, Application Domain, Technology Topic, Popular Technical Reports.
© 2025 PatSnap. All rights reserved.Legal|Privacy policy|Modern Slavery Act Transparency Statement|Sitemap|About US| Contact US: help@patsnap.com