Welding quality evaluation method and system based on ultrasonic image feature fusion
A welding quality and feature fusion technology, applied in welding equipment, non-electric welding equipment, metal processing equipment, etc., can solve the problems of large amount of data, low analysis efficiency, and difficulty in fully characterizing the distribution characteristics of welding defects. Evaluate the effect of comprehensive information
- Summary
- Abstract
- Description
- Claims
- Application Information
AI Technical Summary
Problems solved by technology
Method used
Image
Examples
Embodiment 1
[0078] A welding quality evaluation method based on 3D ultrasonic image feature fusion, such as figure 1 As shown, the method is as follows: first, use a high-frequency ultrasonic microscope to perform ultrasonic inspection on the backfill friction stir spot welding joint, and collect ultrasonic B-scan images and C-scan images of the welding area; then, analyze the obtained ultrasonic B-scan images Analyze and process with the C-scan image, extract the effective information in the image and the defect features inside the solder joint, including the ring width in the C-scan image, the largest defect area, the average defect area and the defect depth in the B-scan image, thus forming The three-dimensional information representation of the welding quality is obtained; on this basis, the information entropy is used to assign different weight coefficients to the extracted three-dimensional feature quantities, and these feature quantities are fused into a comprehensive index, which i...
PUM
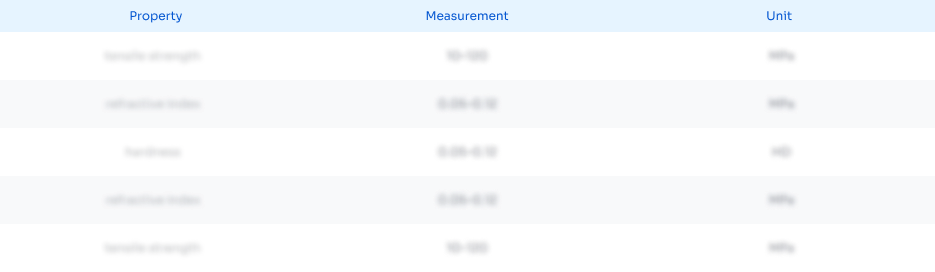
Abstract
Description
Claims
Application Information

- R&D
- Intellectual Property
- Life Sciences
- Materials
- Tech Scout
- Unparalleled Data Quality
- Higher Quality Content
- 60% Fewer Hallucinations
Browse by: Latest US Patents, China's latest patents, Technical Efficacy Thesaurus, Application Domain, Technology Topic, Popular Technical Reports.
© 2025 PatSnap. All rights reserved.Legal|Privacy policy|Modern Slavery Act Transparency Statement|Sitemap|About US| Contact US: help@patsnap.com