Auxiliary positioning mechanism for industrial welding machine
An auxiliary positioning and welding mechanism technology, applied in welding/cutting auxiliary equipment, auxiliary devices, welding equipment, etc., can solve the problems of welding position offset, sliding is not flexible enough, poor positioning effect, etc., to achieve diverse positioning and structural composition Simple, structured effect
- Summary
- Abstract
- Description
- Claims
- Application Information
AI Technical Summary
Problems solved by technology
Method used
Image
Examples
Embodiment
[0031] Embodiment: according to specification Figure 1-6 It can be seen that this case is an auxiliary positioning mechanism for industrial welding machines, including a mounting base 1, two pairs of legs 2 and a support frame 3, two pairs of legs 2 are provided on the bottom surface of the mounting base 1, and a support frame is provided on the top side of the mounting base 1 3. The support frame 3 is provided with a welding mechanism, and a steering movable structure is provided between the support frame 3 and the welding mechanism. The sliding structure and the fixed structure installed on the planar sliding structure, in the specific implementation process, the installation base 1 is supported by the bracket to raise the overall height of the equipment, the support frame 3 is a steel frame with a columnar structure, and the support frame 3 Support the welding mechanism and the steering movable structure, the steering movable structure fixes the welding mechanism, realizes...
PUM
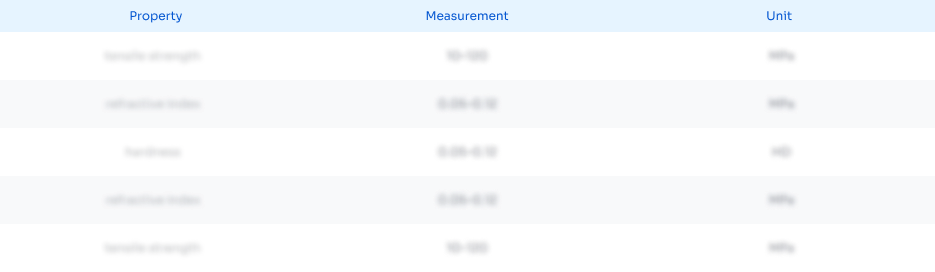
Abstract
Description
Claims
Application Information

- R&D Engineer
- R&D Manager
- IP Professional
- Industry Leading Data Capabilities
- Powerful AI technology
- Patent DNA Extraction
Browse by: Latest US Patents, China's latest patents, Technical Efficacy Thesaurus, Application Domain, Technology Topic, Popular Technical Reports.
© 2024 PatSnap. All rights reserved.Legal|Privacy policy|Modern Slavery Act Transparency Statement|Sitemap|About US| Contact US: help@patsnap.com