Multi-dimensional Force Sensor Structure of Parallel Bar System
A multi-dimensional force sensor and multi-dimensional force technology, applied in the field of sensor measurement, can solve problems such as low multi-dimensional force accuracy, and achieve the effects of improving measurement accuracy and structural rigidity
- Summary
- Abstract
- Description
- Claims
- Application Information
AI Technical Summary
Problems solved by technology
Method used
Image
Examples
specific Embodiment approach 1
[0074] This embodiment is a parallel rod system multi-dimensional force sensor structure, including a support platform and a load platform. The load platform and the support platform are connected through a parallel rod system, and each rod of the parallel rod system is set as an independent strain beam between the load platform and the load platform. Between the support platforms, the external force on the load platform is completely transmitted to the support platform by the parallel rod system; the parallel rod system can be composed of one to any number of strain beams;
[0075] A micro-displacement sensor for measuring the micro-displacement between the support platform and the load platform is arranged, and / or, a strain gauge is arranged on the strain beam of the parallel bar system, and / or, a piezoelectric crystal is used as the strain beam .
[0076] The multi-dimensional force on the load platform can be calculated through the deformation of the strain beam, or the mi...
Embodiment
[0152]In order to obtain high measurement accuracy for this type of sensor, it must be ensured that during the measurement process, the multi-dimensional force is transmitted from the load platform to the support platform through the strain beam, and the structural stiffness of all parts of the entire force transmission path needs to remain basically unchanged. However, the contact surfaces of two parts in the usual welding and bolt connection structures are prone to local contact surface disengagement during the entire stress process, which will lead to a sudden change in the contact stiffness of the contact surface, which will reduce the accuracy of the multidimensional force measurement results. The invention guarantees the invariance of the structural rigidity on the force transmission path through various structural design schemes.
[0153] Multi-dimensional mechanical sensors can be divided into 2-dimensional force (plane 2-dimensional force or 1-dimensional force plus 1-...
PUM
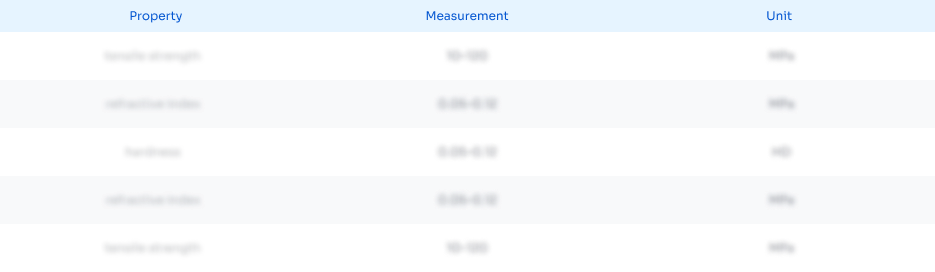
Abstract
Description
Claims
Application Information

- R&D
- Intellectual Property
- Life Sciences
- Materials
- Tech Scout
- Unparalleled Data Quality
- Higher Quality Content
- 60% Fewer Hallucinations
Browse by: Latest US Patents, China's latest patents, Technical Efficacy Thesaurus, Application Domain, Technology Topic, Popular Technical Reports.
© 2025 PatSnap. All rights reserved.Legal|Privacy policy|Modern Slavery Act Transparency Statement|Sitemap|About US| Contact US: help@patsnap.com