Method for quickly optimizing geometric error compensation data of translational axis of five-axis numerical control machine tool
A geometric error, CNC machine tool technology, applied in the direction of program control, mechanical equipment, computer control, etc., can solve problems that affect the production task cycle and execution efficiency, high degree of manual participation, complexity, etc.
- Summary
- Abstract
- Description
- Claims
- Application Information
AI Technical Summary
Problems solved by technology
Method used
Image
Examples
Embodiment 1
[0123] The main process of this embodiment, such as figure 1 As shown, the specific steps are as follows:
[0124] Step 1. Based on the topology structure of the translation axis of the five-axis CNC machine tool and the multi-body system theory, the mathematical relationship between the geometric error term of the translation axis and the spatial positioning error is established. Taking a large-scale gantry five-axis CNC machine tool as an example:
[0125] Step 1.1. Since the spatial positioning error is affected by the geometric error of the translation axis, the figure 2 Describe the geometric error of the translational axis:
[0126] For the feed coordinate axis in the X direction of the machine tool (that is, the X axis), there are three displacement deviation errors: positioning error , straightness error , straightness error ; and 3 rotation angle errors: roll error , pitch error , yaw error .
[0127] In the same way, the 6 geometric errors of the Y ax...
PUM
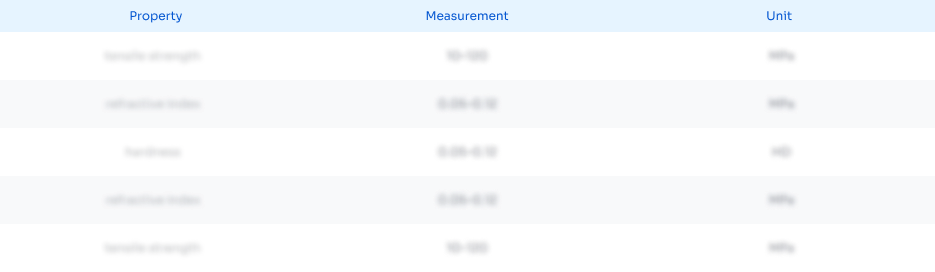
Abstract
Description
Claims
Application Information

- Generate Ideas
- Intellectual Property
- Life Sciences
- Materials
- Tech Scout
- Unparalleled Data Quality
- Higher Quality Content
- 60% Fewer Hallucinations
Browse by: Latest US Patents, China's latest patents, Technical Efficacy Thesaurus, Application Domain, Technology Topic, Popular Technical Reports.
© 2025 PatSnap. All rights reserved.Legal|Privacy policy|Modern Slavery Act Transparency Statement|Sitemap|About US| Contact US: help@patsnap.com