Rotary bidirectional self-locking mechanism
A two-way self-locking and locking technology, applied in the field of mechanical parts, can solve the problems of inability to use robots, loose and falling objects, complex structure, etc., and achieve the effect of eliminating self-locking return clearance, simplifying processing costs, and simplifying processing procedures.
- Summary
- Abstract
- Description
- Claims
- Application Information
AI Technical Summary
Problems solved by technology
Method used
Image
Examples
Embodiment Construction
[0022] The present invention will be further described below in conjunction with the accompanying drawings, but not as a limitation of the present invention.
[0023] It should be noted that all the drawings of the present invention are in simplified form and use inaccurate scales, and are only used to facilitate and clearly assist the purpose of illustrating the embodiments of the present invention.
[0024] see figure 1 , the present invention designs a rotating two-way self-locking mechanism, including an output shaft 1 and an input shaft 2. One end of the output shaft 1 is a shaft hole, and the car has threads for connecting with the load. The other end of the output shaft 1 At one end, a locking part 3 is milled out with a milling cutter for matching with the input shaft. At the same time, the locking part 3 is provided with a mounting hole 3-1 and an assembly groove 3-2, and the mounting hole 3-1 An elastic part 4 is installed, which has the effect of contact self-locki...
PUM
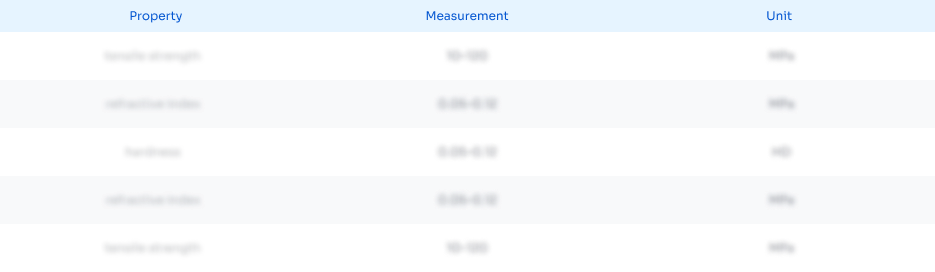
Abstract
Description
Claims
Application Information

- R&D Engineer
- R&D Manager
- IP Professional
- Industry Leading Data Capabilities
- Powerful AI technology
- Patent DNA Extraction
Browse by: Latest US Patents, China's latest patents, Technical Efficacy Thesaurus, Application Domain, Technology Topic, Popular Technical Reports.
© 2024 PatSnap. All rights reserved.Legal|Privacy policy|Modern Slavery Act Transparency Statement|Sitemap|About US| Contact US: help@patsnap.com