Cotton breakage preventing and impurity removing device
An anti-break, cotton technology, used in textiles and papermaking, fiber processing, fiber cleaning machines, etc., can solve the problems of cotton filament tearing, short cotton filament, and reducing cotton processing quality.
- Summary
- Abstract
- Description
- Claims
- Application Information
AI Technical Summary
Problems solved by technology
Method used
Image
Examples
specific Embodiment approach 1
[0040] Combine below Figure 1-17 Description of this embodiment, a cotton anti-breakage and impurity removal device, including a primary conveying mechanism 1, a thickness adaptation mechanism 2, a cotton mass flattening mechanism 3, an elongated output mechanism 4, a lifting mechanism 5, and an impurity removal mechanism 6. The thickness adaptation mechanism 2 is fixedly installed on the primary conveying mechanism 1, the cotton ball flattening mechanism 3 is fixedly installed on the thickness adaptation mechanism 2, the elongation output mechanism 4 is fixedly installed on the thickness adaptation mechanism 2, and the elongation output mechanism 4 is fixedly installed on the On the primary conveying mechanism 1 , the lifting mechanism 5 is fixedly installed on the primary conveying mechanism 1 , and the impurity removal mechanism 6 is fixedly installed on the lifting mechanism 5 .
specific Embodiment approach 2
[0042] Combine below Figure 1-17 Describe this embodiment, this embodiment will further explain the first embodiment, the primary conveying mechanism 1 includes a collective mounting frame 1-1, an upper transmission shaft 1-2, a lower transmission shaft 1-3, a motor one 1-4, Upper gear 1-5, lower gear 1-6, motor one 1-4 are fixedly installed on the through hole that is provided with on the collective mounting bracket 1-1, the output end of motor one 1-4 is fixedly installed with upper gear 1-5, The other side of upper gear 1-5 is fixedly installed with upper transmission shaft 1-2, and the other end of upper transmission shaft 1-2 is rotatably installed in the groove that is provided with on collective installation frame 1-1, and upper gear 1-5 and The lower gears 1-6 are meshed, one side of the lower gears 1-6 is rotatably installed in the groove provided on the collective mounting frame 1-1, and the other side of the lower gears 1-6 is fixedly installed with the lower trans...
specific Embodiment approach 3
[0044] Combine below Figure 1-17 Describe this embodiment, this embodiment will further explain the second embodiment, the thickness adaptation mechanism 2 includes an upper mounting plate 2-1, a lower mounting plate 2-2, an upper fixing plate 2-3, a lower fixing plate 2- 4. Motor two 2-5, chain one 2-6, sprocket one 2-7, two-way threaded rod one 2-8, sprocket two 2-9, two-way threaded rod two 2-10, upper mounting plate 2-1 Slidingly installed in the groove provided on the upper fixed plate 2-3, the lower installed plate 2-2 is slidably installed in the groove provided on the lower fixed plate 2-4, the upper fixed plate 2-3 and the lower fixed plate 2-4 All are fixedly installed on the collective mounting frame 1-1, and one end of two-way threaded rod one 2-8 is rotatably installed in the groove provided on the lower fixed plate 2-4, and two-way threaded rod one 2-8 is connected with the lower mounting plate 2-2 Threaded connection, two-way threaded rod one 2-8 is threadedly...
PUM
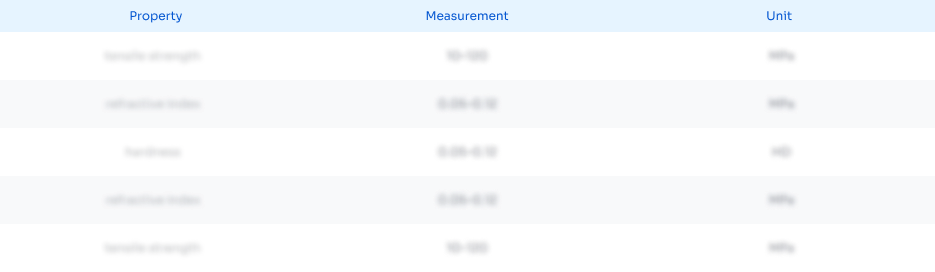
Abstract
Description
Claims
Application Information

- Generate Ideas
- Intellectual Property
- Life Sciences
- Materials
- Tech Scout
- Unparalleled Data Quality
- Higher Quality Content
- 60% Fewer Hallucinations
Browse by: Latest US Patents, China's latest patents, Technical Efficacy Thesaurus, Application Domain, Technology Topic, Popular Technical Reports.
© 2025 PatSnap. All rights reserved.Legal|Privacy policy|Modern Slavery Act Transparency Statement|Sitemap|About US| Contact US: help@patsnap.com