Universal die cutting machining process for solving hole waste discharge
A processing technology, die-cutting technology, applied in the direction of metal processing, etc., can solve the problems of high production cost, high non-discharge rate of waste film, and incomplete waste discharge, etc., to achieve good waste discharge effect, good versatility, and high-quality products good yield
- Summary
- Abstract
- Description
- Claims
- Application Information
AI Technical Summary
Problems solved by technology
Method used
Image
Examples
Embodiment Construction
[0013] A general die-cutting process for solving hole waste, see figure 1 : It includes a roller knife 1 for die-cutting, a conveying track 2 for conveying products, an adsorption device 3 is arranged behind the conveying track 2 corresponding to the product conveying of the roller knife 1, and the die-cutting of the product toward the adsorption device 3 The removal surface is provided with a waste suction tank 4, and the inlet of the inner cavity 5 of the adsorption device 3 is connected to the waste suction tank 4, and the adsorption device 3 also includes a suction device 6, which is connected to the inner cavity 5, and the suction device 6 sucks the product The waste on the surface is adsorbed and then discharged.
[0014] The waste suction device 3 includes a fixed drum 7, a suction pipe 8, and a suction device 6. The die-cutting removal surface of the fixed drum 7 facing the product is provided with a waste suction groove 4, and the length surface of the waste suction g...
PUM
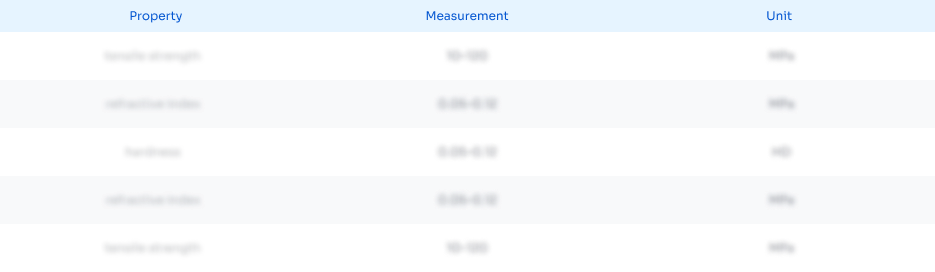
Abstract
Description
Claims
Application Information

- Generate Ideas
- Intellectual Property
- Life Sciences
- Materials
- Tech Scout
- Unparalleled Data Quality
- Higher Quality Content
- 60% Fewer Hallucinations
Browse by: Latest US Patents, China's latest patents, Technical Efficacy Thesaurus, Application Domain, Technology Topic, Popular Technical Reports.
© 2025 PatSnap. All rights reserved.Legal|Privacy policy|Modern Slavery Act Transparency Statement|Sitemap|About US| Contact US: help@patsnap.com