Method for analyzing visual continuousness between uniform parting curved surfaces based on human eye visual limit
A technology of human vision and uniform division, which is applied in image analysis, image data processing, instruments, etc., can solve the problem of not considering the continuity of the curved surfaces on both sides of the slit, and achieve the effect of improving the sense of integrity and the sense of refinement.
- Summary
- Abstract
- Description
- Claims
- Application Information
AI Technical Summary
Problems solved by technology
Method used
Image
Examples
Embodiment example 1
[0048] Implementation case 1: Analysis of the sense of continuity for the 0-point gap between surfaces:
[0049] Step 1: Take points A11 and A12 on the boundary line of a curved surface in the area to be analyzed, and correspondingly take points B11 and B12 on the boundary line of the matching surface, where the distances between A11 and B11, A12 and B12 are all 0. Obtain the curvature of A11 and A12 positions, which are 0.03021mm respectively -1 , 0.004002mm -1 ; Obtain the normal vector differences between A11 and B11, A12 and B12, which are 0.00528° and 0.008925° respectively. Recorded as coordinates: A11B11 (0.03021, 0.00528), A12B12 (0.004002, 0.008925).
[0050] Step 2: Since the gap between surfaces is 0, select the threshold line equation:
[0051] θ=10f 2 +0.001f+0.0001;
[0052] Constructed face-to-face matching continuity analysis model, see image 3 .
[0053] Step 3: Bring the coordinates of the two matching positions A11B11 (0.03021, 0.00528) and A12B12 (0.0...
Embodiment example 2
[0056] Implementation case 2: Analysis of the sense of continuity with a gap of 3 mm between surfaces:
[0057] Step 1: Take points A21 and A22 on the boundary line of a curved surface in the area to be analyzed, and correspondingly take points B21 and B22 on the boundary line of the matching surface, where the distances between A21 and B21, A22 and B22 are all 3mm. Obtain The curvatures at A21 and A22 are 0.01157mm respectively -1 、0.02722mm -1 ; Obtain the normal vector differences between A21 and B21, A22 and B22, which are 4.185° and 47.887° respectively. Recorded as coordinates: A21B21 (0.01157, 4.185°), A22B22 (0.02722, 47.887).
[0058] Step 2: Since the gap between surfaces is 3mm, select the threshold line equation:
[0059] θ=10000f 2 +600f+0.4;
[0060] Build the model.
[0061] The third step: Bring the coordinates of the two matching positions A21B21 (0.01157, 4.185°) and A22B22 (0.02722, 47.887) into the model selected in the second step, and draw the map. ...
Embodiment example 3
[0064] Implementation case 3: Analysis of the sense of continuity for a gap of 6 mm between surfaces:
[0065] Step 1: Take points A31, A32, and A33 on the boundary line of a curved surface in the area to be analyzed, and correspondingly take points B31, B32, and B33 on the boundary line of the matching surface, where A31 and B31, A32 and B32, A33 and The distance of B33 is 6mm. Obtain the curvature of A31, A32, and A33 positions, which are 0.007142mm-1, 0.004178mm-1, and 0.01525mm-1 respectively; obtain the normal vectors of A31 and B31, A32 and B32, A33 and B33 The differences are 6.852°, 40.923°, and 23.541°, respectively. Recorded as coordinates: A31B31 (0.007142, 6.852), A32B32 (0.004178, 40.923), A33B33 (0.01525, 23.541).
[0066] Step 2: Since the gap between surfaces is 6mm, select the threshold line equation:
[0067] θ=40000f 2 +1200f+1;
[0068] Build the model.
[0069] The third step: Bring the coordinates of the three matching positions A31B31 (0.007142, 6.8...
PUM
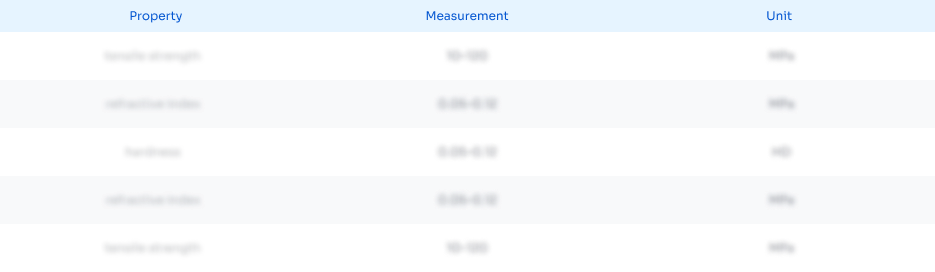
Abstract
Description
Claims
Application Information

- R&D Engineer
- R&D Manager
- IP Professional
- Industry Leading Data Capabilities
- Powerful AI technology
- Patent DNA Extraction
Browse by: Latest US Patents, China's latest patents, Technical Efficacy Thesaurus, Application Domain, Technology Topic, Popular Technical Reports.
© 2024 PatSnap. All rights reserved.Legal|Privacy policy|Modern Slavery Act Transparency Statement|Sitemap|About US| Contact US: help@patsnap.com