A vacuum pump vibration damping device with adjustable stiffness
A vibration damping device and vacuum pump technology, which is applied in the direction of pump components, variable capacity pump components, non-rotational vibration suppression, etc., can solve problems such as difficult adjustment of stiffness, and achieve the effects of improved vibration damping and vibration absorption, small stiffness, and simple and convenient operation
- Summary
- Abstract
- Description
- Claims
- Application Information
AI Technical Summary
Problems solved by technology
Method used
Image
Examples
Embodiment
[0047] The invention provides a vacuum pump damping device with adjustable stiffness, such as Figure 1 to Figure 8 As shown, it includes a pressing part 20 , a washer 30 and a first damping part 40 . Such as Figure 5 As shown, the pressing member 20 is designed as a bowl-shaped structure as a whole, and a plurality of claws 22 are uniformly arranged along the circumferential direction in the bottom of the bowl-shaped structure. A flange is provided on the mouth of the bowl-shaped structure, and three evenly distributed installation holes are opened on the flange.
[0048] Such as Figure 4 As shown, the first shock absorber 40 is designed as a ring structure as a whole, the surface area of the ring structure matches the surface area of the bottom of the bowl-shaped structure of the pressing member 20, and the first shock absorber 40 is connected to the end of the vacuum pump 50 motor. The surface areas in contact with each other are equal. Grooves 42 respectively cor...
PUM
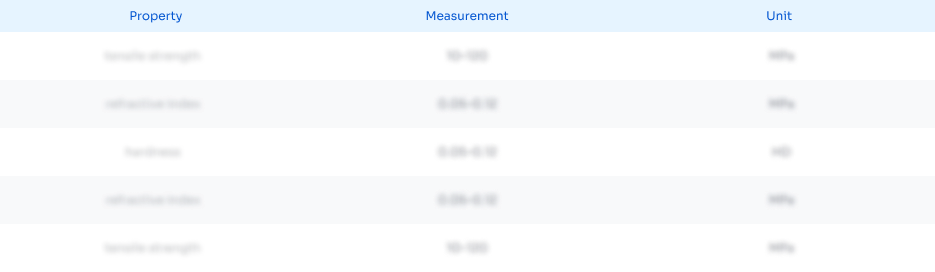
Abstract
Description
Claims
Application Information

- R&D
- Intellectual Property
- Life Sciences
- Materials
- Tech Scout
- Unparalleled Data Quality
- Higher Quality Content
- 60% Fewer Hallucinations
Browse by: Latest US Patents, China's latest patents, Technical Efficacy Thesaurus, Application Domain, Technology Topic, Popular Technical Reports.
© 2025 PatSnap. All rights reserved.Legal|Privacy policy|Modern Slavery Act Transparency Statement|Sitemap|About US| Contact US: help@patsnap.com