A Cylinder-Based Variable Stiffness Joint System
A technology of variable stiffness and cylinder, applied in the field of robots, can solve the problems of narrow joint deformation range, large joint size, and many parts, and achieve the effect of reducing joint weight, reducing joint size, and high adaptability
- Summary
- Abstract
- Description
- Claims
- Application Information
AI Technical Summary
Problems solved by technology
Method used
Image
Examples
Embodiment Construction
[0023] The present invention will be further described in detail with reference to the accompanying drawings and embodiments.
[0024] The present invention is a cylinder-based variable stiffness joint system, such as figure 1 As shown, it includes: cylinder support plate 1, upper cylinder 2, support plate connecting rod 3, lower cylinder 4, lower linear displacement sensor 5, transmission spindle 6, arm connection block 7, rack support plate 8, upper linear displacement sensor 9 , upper proportional valve 10, air source 11, computer 12, lower proportional valve 13, upper sensor connection block 14, upper sensor connection base 15, upper rack 16, transmission gear 17, lower rack 18, lower sensor connection base 19, Lower sensor connection block 20, lower cylinder connection block 21, lower linear guide rail 22, lower cylinder connection base 23, upper cylinder connection block 24, upper linear guide rail 25, upper cylinder connection base 26, motor 27;
[0025] The cylinder-b...
PUM
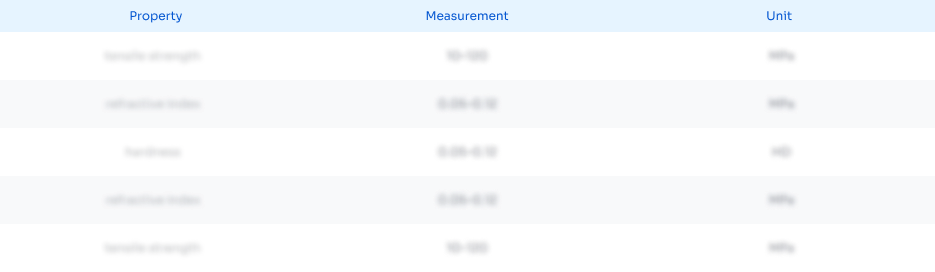
Abstract
Description
Claims
Application Information

- R&D Engineer
- R&D Manager
- IP Professional
- Industry Leading Data Capabilities
- Powerful AI technology
- Patent DNA Extraction
Browse by: Latest US Patents, China's latest patents, Technical Efficacy Thesaurus, Application Domain, Technology Topic, Popular Technical Reports.
© 2024 PatSnap. All rights reserved.Legal|Privacy policy|Modern Slavery Act Transparency Statement|Sitemap|About US| Contact US: help@patsnap.com