Dynamic torque control method capable of tracking optimal modal gain based on air density
A technology of torque control and air density, which is applied in the direction of engine control, wind engine control, engine, etc., can solve the problems of reduced fan operation output efficiency and reduced power generation of wind turbines, and achieves the effect of improving wind energy utilization efficiency
- Summary
- Abstract
- Description
- Claims
- Application Information
AI Technical Summary
Problems solved by technology
Method used
Image
Examples
Embodiment 1
[0033] Such as figure 1 As shown, a dynamic torque control method based on air density tracking optimal modal gain, specifically includes the following steps:
[0034] Step S1: The main control system obtains the current real-time wind speed, and judges whether it is higher than the preset rated wind speed, if it is higher, go to step S4, otherwise go to step S2;
[0035] Step S2: The torque control module obtains the current air density value and the angular velocity of the blade rotation of the wind turbine, calculates the optimal torque control coefficient according to the air density value and the angular velocity of the blade rotation, and sends the optimal torque control coefficient to main control system;
[0036] Step S3: The main control system adjusts the tip speed ratio of the wind rotor according to the optimal tip speed ratio corresponding to the received optimal torque control coefficient, so as to realize the maximum capture of wind energy;
[0037] Step S4: T...
PUM
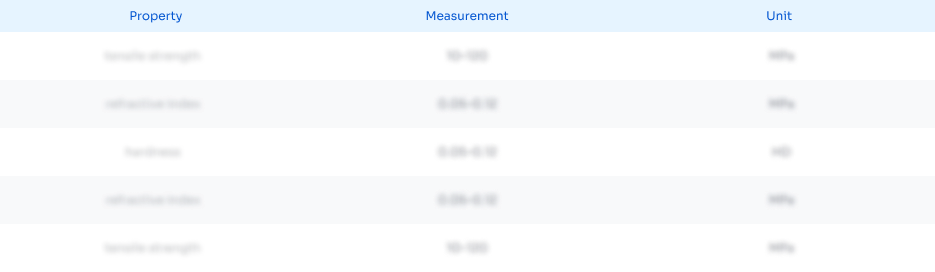
Abstract
Description
Claims
Application Information

- R&D Engineer
- R&D Manager
- IP Professional
- Industry Leading Data Capabilities
- Powerful AI technology
- Patent DNA Extraction
Browse by: Latest US Patents, China's latest patents, Technical Efficacy Thesaurus, Application Domain, Technology Topic, Popular Technical Reports.
© 2024 PatSnap. All rights reserved.Legal|Privacy policy|Modern Slavery Act Transparency Statement|Sitemap|About US| Contact US: help@patsnap.com