Robot external active gravity compensation system and simulation verification method
A technology of gravity compensation and simulation verification, applied in the field of robots, can solve the problems of poor end joint compensation effect, increase robot mass and inertia, reduce joint response ability, etc., to reduce joint load and expand application scenarios.
- Summary
- Abstract
- Description
- Claims
- Application Information
AI Technical Summary
Problems solved by technology
Method used
Image
Examples
Embodiment Construction
[0038] The present invention will be further described below in conjunction with accompanying drawing:
[0039] Such as figure 1 As shown: the present invention includes a gravity compensation device 2 and a gravity compensation rope 3, the force end of the gravity compensation device 2 is connected to one end of the gravity compensation rope 2, and the other end of the gravity compensation rope 2 is connected to the force end of the serial robot 1 , the force application end of the serial robot 1 is connected to the end load 4 at the same time.
[0040] When using a small 6R robot to complete the assembly task of large-mass parts, in order to ensure the freedom of movement of the robot, an external gravity compensation system is used to directly compensate the gravity of the large-mass load at the end. The structure of robot and gravity compensation system is as follows: figure 1 shown. A variable-length belt-driven rope is used to connect the end of the robot to the end o...
PUM
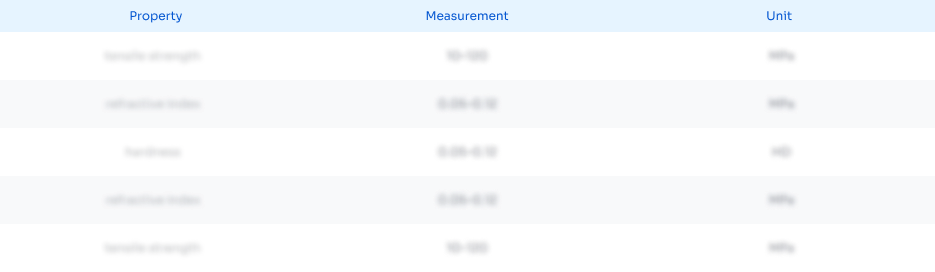
Abstract
Description
Claims
Application Information

- R&D
- Intellectual Property
- Life Sciences
- Materials
- Tech Scout
- Unparalleled Data Quality
- Higher Quality Content
- 60% Fewer Hallucinations
Browse by: Latest US Patents, China's latest patents, Technical Efficacy Thesaurus, Application Domain, Technology Topic, Popular Technical Reports.
© 2025 PatSnap. All rights reserved.Legal|Privacy policy|Modern Slavery Act Transparency Statement|Sitemap|About US| Contact US: help@patsnap.com