A mold core processing device for manufacturing a gradually changing angle light guide plate
A processing device and light guide plate technology, which is applied in the direction of manufacturing tools, household appliances, and other household appliances, can solve the problems of mold core burrs, waste, etc., and achieve the effects of saving costs, changing the vibration intensity, and improving the coating effect
- Summary
- Abstract
- Description
- Claims
- Application Information
AI Technical Summary
Problems solved by technology
Method used
Image
Examples
Embodiment Construction
[0033] see Figure 1~5 , in an embodiment of the present invention, a mold core processing device for manufacturing a light guide plate with a gradual angle, which includes a machine body 1, an oscillating uniform liquid component 2, a processing table 3, a mold core 4, and a burr repair component 5, wherein , the oscillating uniform liquid component 2 is arranged in the body 1, and the oscillating end of the oscillating liquid uniform component 2 is connected to a processing table 3, and a mold core 4 is fixed on the processing table 3, and the mold core 4 The burr repair assembly 5 is arranged above;
[0034] The burr repair component 5 can sequentially provide coating, sandblasting and polishing for the mold core;
[0035] Wherein, when the burr repairing component 5 sprays liquid and coats the mold core, the oscillating uniform liquid component 2 can drive the mold core 4 to vibrate at the same time, so that the coating liquid does not adhere to the burrs higher than the ...
PUM
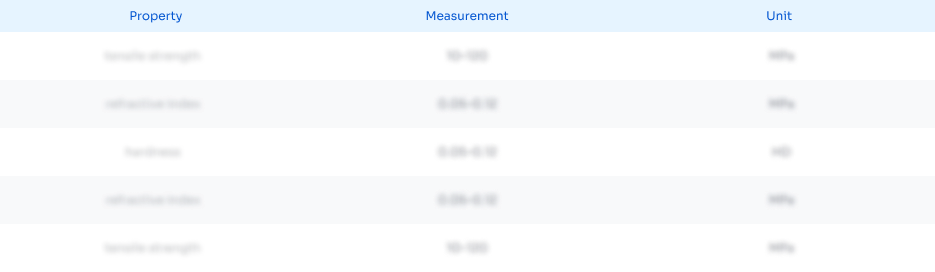
Abstract
Description
Claims
Application Information

- R&D
- Intellectual Property
- Life Sciences
- Materials
- Tech Scout
- Unparalleled Data Quality
- Higher Quality Content
- 60% Fewer Hallucinations
Browse by: Latest US Patents, China's latest patents, Technical Efficacy Thesaurus, Application Domain, Technology Topic, Popular Technical Reports.
© 2025 PatSnap. All rights reserved.Legal|Privacy policy|Modern Slavery Act Transparency Statement|Sitemap|About US| Contact US: help@patsnap.com