Obstacle crossing wheel device and self-walking robot
An obstacle-crossing wheel and robot technology, applied in the field of robots, can solve the problems of limited friction, low obstacle-crossing ability, and the groove cannot be made too deep, and achieves the effects of high reliability, low cost and simple structure.
- Summary
- Abstract
- Description
- Claims
- Application Information
AI Technical Summary
Problems solved by technology
Method used
Image
Examples
no. 1 example
[0052] see Figure 1 to Figure 4 , The legs 21 and the wheel body 10 are combined with each other. Specifically, the outer edge portion 11 is formed with a chute 110 passing through the outer edge portion 11, and the legs 21 are slidably inserted in the chute 110, that is to say, the legs 21 are located inside the outer edge portion 11, and the legs 21 In the process of extending outward along the wheel body 10 , the outer edge portion 11 needs to be penetrated.
[0053] In this embodiment, the elastic member 22 applies a force toward the outside of the wheel body 10 to the leg 21 in a compressed state. Specifically, in this embodiment, the elastic member 22 is a compression spring 22', and the compression spring 22' can make the supporting leg 21 have a larger sliding range.
[0054] see figure 1 The mounting seat 23 includes a guide sleeve 231 and a seat body 232 , wherein the seat body 232 is located on the inside of the guide sleeve 231 along the wheel body 10 , and the...
no. 2 example
[0062] see Figure 5 , the structure of this embodiment is generally the same as that of the first embodiment. The difference from the first embodiment is that in this embodiment, the elastic member 22 exerts an effect on the leg 21 towards the outside of the wheel body 10 in a stretched state. force. This embodiment is described by taking the elastic member 22 as a tension spring 22" as an example.
[0063] In this embodiment, the mounting base 23 is roughly in the shape of a sleeve, one side of the mounting base 23 is fastened to the periphery of the chute 110, the avoidance hole 23b communicates with the chute 110 and is arranged coaxially, and the elastic member 22 is clamped at the limit Between the portion 212 and the inner surface of the outer edge portion 11 , opposite sides of the elastic member 22 are fastened to the limiting portion 212 and the outer edge portion 11 respectively. When the obstacle-crossing wheel device is not subjected to external force, the elast...
no. 3 example
[0065] see Figure 6 to Figure 9The structure of this embodiment is generally the same as that of the first embodiment. The difference from the first embodiment is that the legs 21 are relatively independent from the wheel body 10. Specifically, the legs 21 are located at one side of the outer edge 11 along the rotation axis L. On the side, when the supporting legs 21 protrude outward along the wheel body 10 , they will not contact the outer edge portion 11 or interfere with the outer edge portion 11 . That is to say, in the third embodiment, the sliding groove 110 in the first embodiment is not provided on the outer edge portion 11 .
[0066] Specifically, in this embodiment, the guide sleeve 231 is disposed on the circumferential surface of the seat body 232, the elastic member 22 and the limiting portion 212 are located in the accommodating cavity 23a, the limiting portion 212 can abut against the surrounding of the escape hole 23b, and the elastic member 22 abuts between ...
PUM
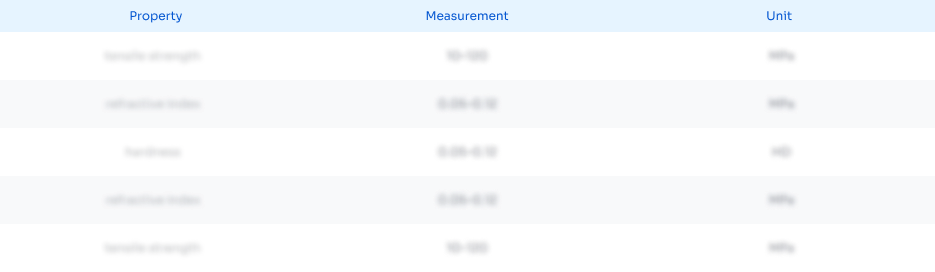
Abstract
Description
Claims
Application Information

- R&D Engineer
- R&D Manager
- IP Professional
- Industry Leading Data Capabilities
- Powerful AI technology
- Patent DNA Extraction
Browse by: Latest US Patents, China's latest patents, Technical Efficacy Thesaurus, Application Domain, Technology Topic, Popular Technical Reports.
© 2024 PatSnap. All rights reserved.Legal|Privacy policy|Modern Slavery Act Transparency Statement|Sitemap|About US| Contact US: help@patsnap.com