Crease-resistant textile winding drum and method applied to textile
A textile and textile technology, applied in the field of textiles, can solve problems such as fabric wrinkles and affect the winding effect of the reel, and achieve the effects of avoiding wrinkles, improving the winding effect, and avoiding mutual friction
- Summary
- Abstract
- Description
- Claims
- Application Information
AI Technical Summary
Problems solved by technology
Method used
Image
Examples
Embodiment 1
[0066] A wrinkle-resistant textile reel applied to textiles, such as figure 1 As shown, it includes a cylinder body 10 installed between side plates 20 , and a rotating shaft 30 is provided at the side end of the side plate 20 . The cylinder body 10 includes: a main module 40 , a sub-module 50 , and a clamping block 60 .
[0067] Such as figure 1 , 3 As shown, the main module 40 is fixed in the middle of the chute 11 arranged transversely on the barrel 10 .
[0068] Such as Figure 4-6 As shown, the sub-module 50 is slidingly connected to the chute 11 of the cylinder body 10, the sub-module 50 is located on both sides of the main module 40, and the sub-module 50 has: a sub-material port 51, a first sub-pressure groove 52, a first sub-slide 54 , pressure column 56, secondary runner 58.
[0069] The auxiliary material opening 51 is laterally aligned with the main material opening 41 of the main module 40 . The first auxiliary pressure groove 52 is arranged on the side of th...
Embodiment 2
[0086] A wrinkle-resistant textile reel applied to textiles has the same characteristic structure as that of Embodiment 1, wherein, as Figure 9 As shown, a flexible layer 63 is provided on opposite surfaces of the two clamping blocks 60, and an empty bag 64 is arranged in the flexible layer 63, and the empty bag 64 is circular. The side end of the empty bag 64 is provided with a fixed limiting plate 65 , the limiting plate 65 is located on the same side of the empty bag 64 , and the empty bag 64 and the limiting plate 65 are in close contact with each other.
[0087] During the clamping process of the cloth by the clamping block 60, the flexible layers 63 on the opposite sides of the two clamping blocks 60 are pressed against each other and are stressed. The limiting plate 65 on the side restricts the empty bag 64, therefore, the empty bag 64 can only be deformed to the same side direction, and then the deformation direction of the flexible layer 63 is biased to the same dire...
Embodiment 3
[0089] An anti-wrinkle method applied to textiles, comprising the following steps:
[0090] When the cloth needs to be clamped, insert the head of the cloth into the main material opening 41 of the main module 40 and the auxiliary material openings 51 of the sub-module 50 on both sides of the main module 40, so that the pressure between the cloth and the sub-module 50 The columns 56 are opposite, and then the secondary runner 58 is rotated to push the pressure column 56 on the first secondary connecting rod 561, and the cloth is pressed into the first secondary pressure groove 52, so that the cloth is in close contact with the pressure column 56, wherein the main module 40 pairs The sub-module 50 is positioned so that when the sub-module 50 slides to both sides, it can be carried out synchronously, which is conducive to ensuring the center position of the cloth and the cylinder body 10, improving the winding effect, and avoiding the friction between the cloth and the side plate...
PUM
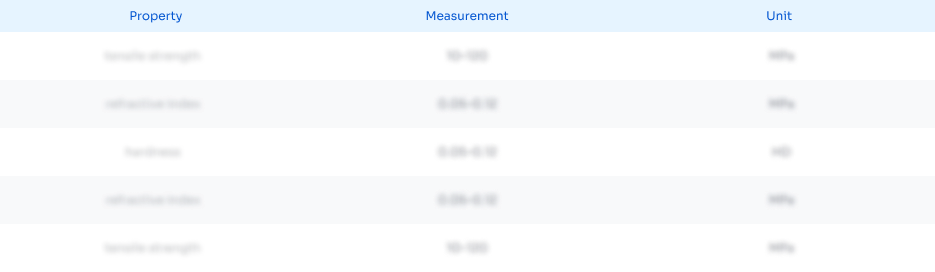
Abstract
Description
Claims
Application Information

- Generate Ideas
- Intellectual Property
- Life Sciences
- Materials
- Tech Scout
- Unparalleled Data Quality
- Higher Quality Content
- 60% Fewer Hallucinations
Browse by: Latest US Patents, China's latest patents, Technical Efficacy Thesaurus, Application Domain, Technology Topic, Popular Technical Reports.
© 2025 PatSnap. All rights reserved.Legal|Privacy policy|Modern Slavery Act Transparency Statement|Sitemap|About US| Contact US: help@patsnap.com