Shock absorber signal disc structure
A shock absorber and signal plate technology, applied in the design characteristics of spring/shock absorber, spring/shock absorber, machine/engine, etc., can solve the problems of insufficient connection and troublesome installation, and achieve convenient installation and weight reduction. Cost, effect of reducing angle deviation
- Summary
- Abstract
- Description
- Claims
- Application Information
AI Technical Summary
Problems solved by technology
Method used
Image
Examples
Embodiment Construction
[0019] Below in conjunction with embodiment, the present invention is further described, but does not constitute any restriction to the present invention, anyone makes the limited number of amendments in the scope of claims of the present invention, still within the scope of claims of the present invention.
[0020] The specific embodiment of the present invention is like this: with reference to Figure 1-3 As shown, a signal plate structure of a shock absorber includes a shock absorber outer ring 1, a wheel groove 15, a rubber part 2, a shock absorber inner ring 3, a crankshaft 4, a positioning pin 5 and a connecting bolt 6, and the wheel groove 15 is set On the outer ring 1 of the shock absorber, the outer ring 1 of the shock absorber is sleeved on the rear end of the inner ring 3 of the shock absorber, and the rubber part 2 is arranged between the inner wall of the outer ring 1 of the shock absorber and the outer wall of the inner ring 3 of the shock absorber The inner ring...
PUM
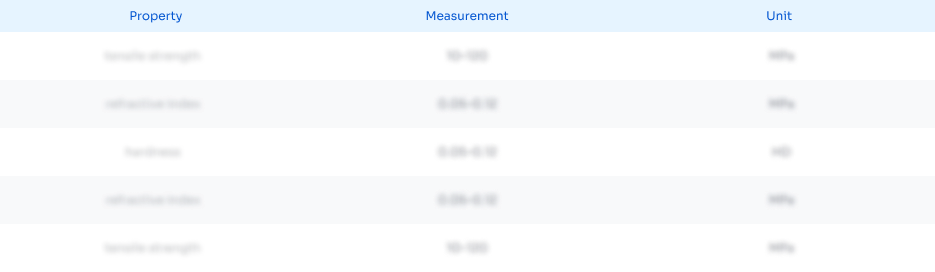
Abstract
Description
Claims
Application Information

- R&D
- Intellectual Property
- Life Sciences
- Materials
- Tech Scout
- Unparalleled Data Quality
- Higher Quality Content
- 60% Fewer Hallucinations
Browse by: Latest US Patents, China's latest patents, Technical Efficacy Thesaurus, Application Domain, Technology Topic, Popular Technical Reports.
© 2025 PatSnap. All rights reserved.Legal|Privacy policy|Modern Slavery Act Transparency Statement|Sitemap|About US| Contact US: help@patsnap.com