Aerospace model flight test layout, and axisymmetric nose cone area configuration and design method thereof
A flight test, axisymmetric technology, applied in special data processing applications, geometric CAD, constraint-based CAD, etc., can solve the problems of long design cycle, high development cost, and long cycle of experimental model, so as to shorten the design cycle, reduce The effect of design cost and workload reduction
- Summary
- Abstract
- Description
- Claims
- Application Information
AI Technical Summary
Problems solved by technology
Method used
Image
Examples
Embodiment Construction
[0043] All features disclosed in this specification, or steps in all methods or processes disclosed, may be combined in any manner, except for mutually exclusive features and / or steps.
[0044] Any feature disclosed in this specification (including any appended claims, abstract and drawings), unless expressly stated otherwise, may be replaced by alternative features which are equivalent or serve a similar purpose. That is, unless expressly stated otherwise, each feature is one example only of a series of equivalent or similar features.
[0045]First of all, according to the mission requirements of the aerospace model flight test, select a suitable and mature axisymmetric booster as the basic platform for the flight test. When selecting the test platform, it needs to be comprehensively selected from the aspects of power, structure, control, etc. In this embodiment, the selected The diameter of the rocket engine is 0.375mm, and the nose cone length of the aircraft is 1471.5mm. T...
PUM
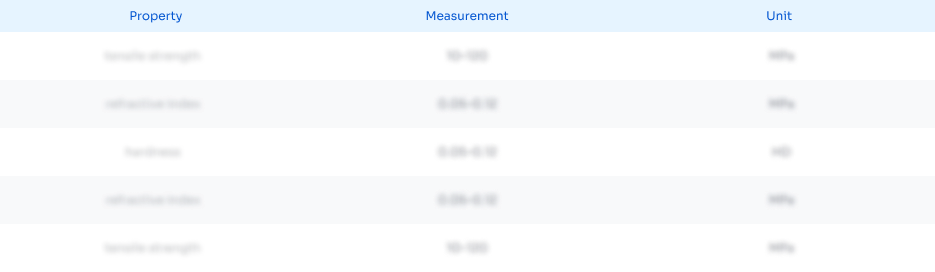
Abstract
Description
Claims
Application Information

- Generate Ideas
- Intellectual Property
- Life Sciences
- Materials
- Tech Scout
- Unparalleled Data Quality
- Higher Quality Content
- 60% Fewer Hallucinations
Browse by: Latest US Patents, China's latest patents, Technical Efficacy Thesaurus, Application Domain, Technology Topic, Popular Technical Reports.
© 2025 PatSnap. All rights reserved.Legal|Privacy policy|Modern Slavery Act Transparency Statement|Sitemap|About US| Contact US: help@patsnap.com