Three-degree-of-freedom hybrid magnetic bearing rotor displacement self-detection method
A technology of hybrid magnetic bearings and degrees of freedom, applied in mechanical bearing testing, measuring devices, using electromagnetic means, etc., can solve problems such as local optimum and slow convergence speed
- Summary
- Abstract
- Description
- Claims
- Application Information
AI Technical Summary
Problems solved by technology
Method used
Image
Examples
Embodiment Construction
[0049] In order to make the object, technical solution and effect of the present invention clearer and clearer, the following examples are given to further describe the present invention in detail. It should be pointed out that the specific implementations described here are only used to explain the present invention, not to limit the present invention.
[0050] In the present invention, the magnetic bearing control current is used as the input sample, and the radial and axial displacements are used as the output sample to collect sample data, select a mixed kernel function, optimize the performance parameters of the support vector machine through the particle swarm algorithm, and use the training samples and performance parameters to train the minimum quadratic Multiply the support vector machine to establish a nonlinear prediction model, connect the prediction model in series to the three-degree-of-freedom AC-DC hybrid magnetic bearing, connect it to the linear closed-loop co...
PUM
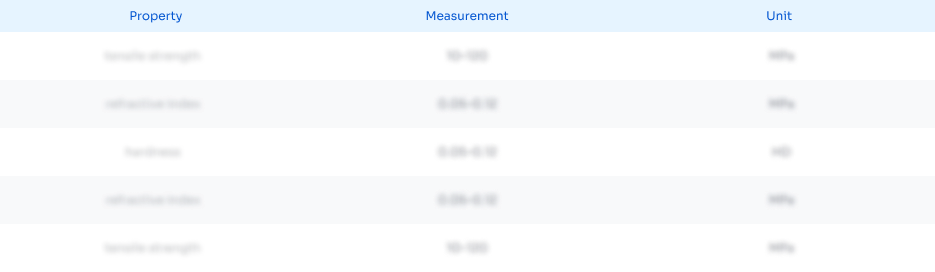
Abstract
Description
Claims
Application Information

- R&D Engineer
- R&D Manager
- IP Professional
- Industry Leading Data Capabilities
- Powerful AI technology
- Patent DNA Extraction
Browse by: Latest US Patents, China's latest patents, Technical Efficacy Thesaurus, Application Domain, Technology Topic, Popular Technical Reports.
© 2024 PatSnap. All rights reserved.Legal|Privacy policy|Modern Slavery Act Transparency Statement|Sitemap|About US| Contact US: help@patsnap.com