Double-hearth shaft kiln and calcining method
A double-chamber shaft kiln and shaft kiln technology, which is applied in the field of industrial furnaces and kilns, can solve problems such as affecting the calcining quality of products, failure of calcining materials, and deviation of hot air flow.
- Summary
- Abstract
- Description
- Claims
- Application Information
AI Technical Summary
Problems solved by technology
Method used
Image
Examples
Embodiment Construction
[0024] It should be noted that, in the case of no conflict, the embodiments in the present application and the features in the embodiments can be combined with each other. The present invention will be described in detail below with reference to the accompanying drawings and examples.
[0025] like Figure 1 to Figure 3 As shown, the embodiment of the present invention provides a double-chamber shaft kiln, including a first shaft kiln 1 and a second shaft kiln 2 with the same structure and symmetrically arranged, the first shaft kiln 1 includes a middle kiln chamber 12, and the middle kiln chamber 12 The cross section of is a regular polygon with more than five sides, and the side wall of the middle kiln chamber 12 of the first shaft kiln 1 is connected with the side wall of the middle kiln chamber 12 of the second shaft kiln 2 .
[0026] The side wall of the middle kiln chamber 12 of the first shaft kiln 1 and the side wall of the middle kiln chamber 12 of the second shaft k...
PUM
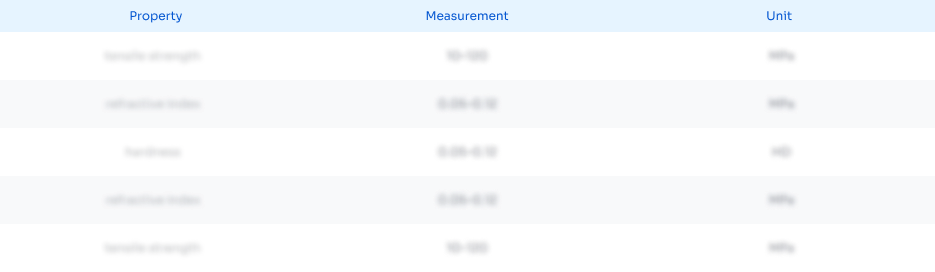
Abstract
Description
Claims
Application Information

- R&D Engineer
- R&D Manager
- IP Professional
- Industry Leading Data Capabilities
- Powerful AI technology
- Patent DNA Extraction
Browse by: Latest US Patents, China's latest patents, Technical Efficacy Thesaurus, Application Domain, Technology Topic, Popular Technical Reports.
© 2024 PatSnap. All rights reserved.Legal|Privacy policy|Modern Slavery Act Transparency Statement|Sitemap|About US| Contact US: help@patsnap.com