Laser machining cooperation method, system, equipment and medium
A laser processing and working technology, applied in laser welding equipment, metal processing equipment, welding equipment and other directions, can solve the problems of repeated processing angle, boundary dislocation, limited laser processing size range, etc., to speed up processing and improve processing efficiency Effect
- Summary
- Abstract
- Description
- Claims
- Application Information
AI Technical Summary
Problems solved by technology
Method used
Image
Examples
Embodiment Construction
[0036] The core of the present invention is to provide a cooperative method, system, equipment and medium for laser processing that can control the processing beam and the mechanical motion platform to perform coordinated and cooperative movements, thereby reducing processing errors.
[0037] In order to enable those skilled in the art to better understand the solution of the present invention, the present invention will be further described in detail below in conjunction with the accompanying drawings and specific embodiments. Apparently, the described embodiments are only some of the embodiments of the present invention, but not all of them. Based on the embodiments of the present invention, all other embodiments obtained by persons of ordinary skill in the art without making creative efforts belong to the protection scope of the present invention.
[0038] The terms "first", "second", "third", "fourth", etc. (if any) in the specification and claims of the present applicatio...
PUM
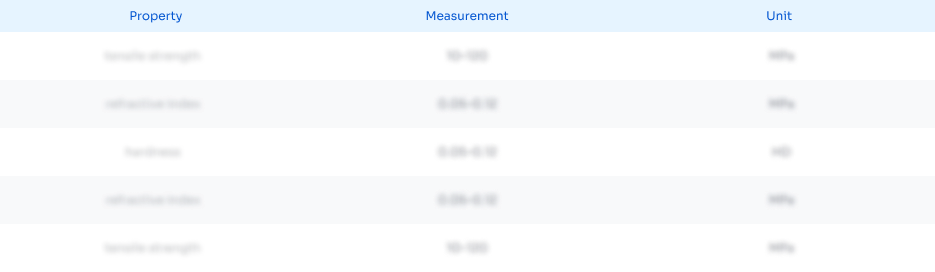
Abstract
Description
Claims
Application Information

- R&D Engineer
- R&D Manager
- IP Professional
- Industry Leading Data Capabilities
- Powerful AI technology
- Patent DNA Extraction
Browse by: Latest US Patents, China's latest patents, Technical Efficacy Thesaurus, Application Domain, Technology Topic, Popular Technical Reports.
© 2024 PatSnap. All rights reserved.Legal|Privacy policy|Modern Slavery Act Transparency Statement|Sitemap|About US| Contact US: help@patsnap.com