Track deformation detection method
A detection method and track technology, applied in measurement devices, instruments, optical devices, etc., can solve problems such as affecting detection accuracy and large errors, and achieve the effects of improving detection accuracy, eliminating calculation errors, and reducing installation work.
- Summary
- Abstract
- Description
- Claims
- Application Information
AI Technical Summary
Problems solved by technology
Method used
Image
Examples
Embodiment 1
[0037] See figure 1 , A method for detecting track deformation, including the following steps:
[0038] a. Install an encoder on the wheel shaft of the crane, and the encoder updates the measurement data following the movement of the crane. The data signal of the encoder is analyzed through PLC and converted into the crane position value to obtain the track detection position value;
[0039] b. Install and fix the measuring trolley under the walking beam of the crane, the wheel groove of the wheel 4 of the measuring trolley is close to the track and level with the track, and then the laser rangefinder 11 and the reflector 12 are installed on the measuring trolley;
[0040] c. The measuring trolley moves along the full stroke of the crane. The beam of the laser rangefinder 11 extends perpendicular to the track direction and irradiates the reflector 12, the reflector 12 reflects the beam, and the laser rangefinder 11 receives the beam and sends it out between the reflector 12. For meas...
Embodiment 2
[0044] See figure 1 , A method for detecting track deformation, including the following steps:
[0045] a. Install an encoder on the wheel shaft of the crane, and the encoder updates the measurement data following the movement of the crane. The data signal of the encoder is analyzed through PLC and converted into the crane position value to obtain the track detection position value;
[0046] b. Install and fix the measuring trolley under the walking beam of the crane, the wheel groove of the wheel 4 of the measuring trolley is close to the track and level with the track, and then the laser rangefinder 11 and the reflector 12 are installed on the measuring trolley;
[0047] c. The measuring trolley moves along the full stroke of the crane. The beam of the laser rangefinder 11 extends perpendicular to the track direction and irradiates the reflector 12, the reflector 12 reflects the beam, and the laser rangefinder 11 receives the beam and sends it out between the reflector 12. For meas...
Embodiment 3
[0052] See figure 1 , A method for detecting track deformation, including the following steps:
[0053] a. Install an encoder on the wheel shaft of the crane, and the encoder updates the measurement data following the movement of the crane. The data signal of the encoder is analyzed through PLC and converted into the crane position value to obtain the track detection position value;
[0054] b. Install and fix the measuring trolley under the walking beam of the crane, the wheel groove of the wheel 4 of the measuring trolley is close to the track and level with the track, and then the laser rangefinder 11 and the reflector 12 are installed on the measuring trolley;
[0055] c. The measuring trolley moves along the full stroke of the crane. The beam of the laser rangefinder 11 extends perpendicular to the track direction and irradiates the reflector 12, the reflector 12 reflects the beam, and the laser rangefinder 11 receives the beam and sends it out between the reflector 12. For meas...
PUM
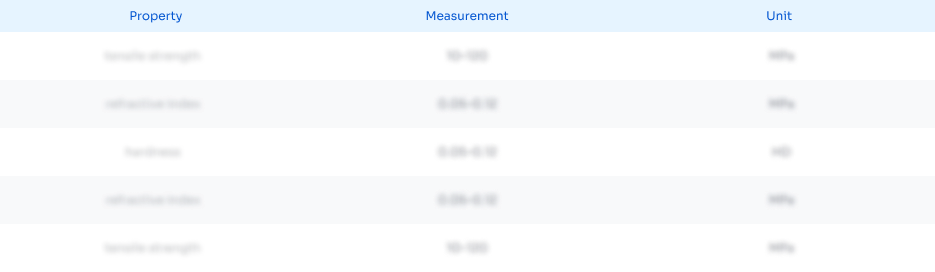
Abstract
Description
Claims
Application Information

- R&D
- Intellectual Property
- Life Sciences
- Materials
- Tech Scout
- Unparalleled Data Quality
- Higher Quality Content
- 60% Fewer Hallucinations
Browse by: Latest US Patents, China's latest patents, Technical Efficacy Thesaurus, Application Domain, Technology Topic, Popular Technical Reports.
© 2025 PatSnap. All rights reserved.Legal|Privacy policy|Modern Slavery Act Transparency Statement|Sitemap|About US| Contact US: help@patsnap.com