Magnetic material tray switch and implementation method thereof
A technology of magnetic materials and switches, applied in the direction of conveyors, conveyor objects, conveyor control devices, etc., can solve problems such as rising defect rate, easy scratches of paint, and many labors
- Summary
- Abstract
- Description
- Claims
- Application Information
AI Technical Summary
Problems solved by technology
Method used
Image
Examples
Embodiment 1
[0045] see Figure 1-10 , the present invention provides the following technical solutions: a magnetic material tray exchange, including a dryer 1 and a conveying line 8 arranged on one side of the dryer 1, an installation frame 4 is arranged above the discharge end of the dryer 1, A tray guide mechanism 6 is connected above the discharge end of the dryer 1, a first transport mechanism 5 is connected above the corresponding tray guide mechanism 6 on the installation frame 4, and a side of the first transport mechanism 5 is connected to the installation frame 4 There is a first transplanting mechanism 3, and the second transporting mechanism 2 is connected to the side where the first transplanting mechanism 3 is away from the first transporting mechanism 5 on the installation frame 4, and the second transporting mechanism 2 is connected on the conveying line 8. Corresponding to the second transplanting mechanism 7, the conveying line 8 is connected with a conveying line tray in...
Embodiment 2
[0058] The difference between this embodiment and Embodiment 1 is that further, the second transplanting mechanism 7 includes a second transplanting mechanism mounting plate 71, a second transplanting cylinder 72, a buffer 73, a tray lifting rod 74, a third Slider slide rail 75 and slide rail mounting plate 76, wherein, the second transplanting mechanism mounting plate 71 is installed on the support of conveying line 8, is connected with the 3rd slide of four symmetrical arrangements on the second transplanting mechanism mounting plate 71. Block slide rail 75, the slide block of the 3rd slide block slide rail 75 is connected on the second transplanting mechanism mounting plate 71, and the lower end of the 3rd slide block slide rail 75 slide rail is connected with slide rail mounting plate 76, is positioned at same side The upper ends of the slide rails of the two third slide block slide rails 75 are connected with the tray lifting rod 74, and the second transplanting mechanism ...
PUM
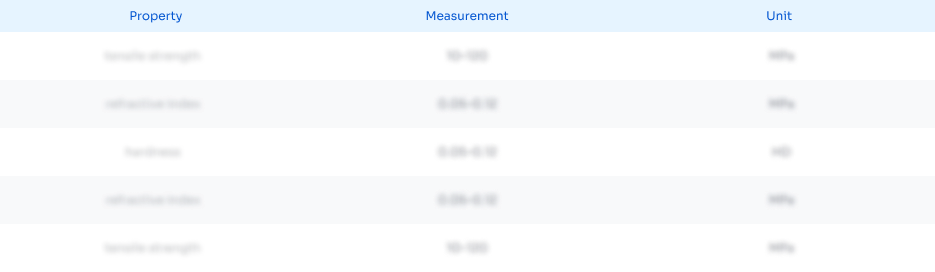
Abstract
Description
Claims
Application Information

- R&D Engineer
- R&D Manager
- IP Professional
- Industry Leading Data Capabilities
- Powerful AI technology
- Patent DNA Extraction
Browse by: Latest US Patents, China's latest patents, Technical Efficacy Thesaurus, Application Domain, Technology Topic, Popular Technical Reports.
© 2024 PatSnap. All rights reserved.Legal|Privacy policy|Modern Slavery Act Transparency Statement|Sitemap|About US| Contact US: help@patsnap.com